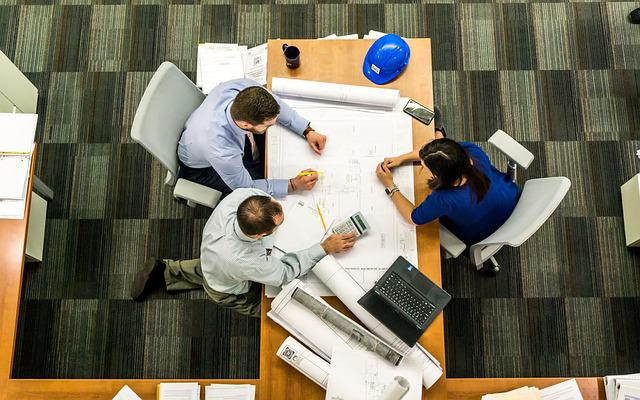
Program management involves managing multiple projects at the same time. To ensure everyone knows their roles and responsibilities, it is important to clearly define the goals and timelines for each project. This ensures that projects are completed on time. Learn more about program administration. We'll discuss the program management process, goals, and tools.
Managing multiple projects at the same time
It is hard to manage multiple projects simultaneously. These tips will help you think strategically and manage multiple projects simultaneously. Be honest with your clients and teammates. This will prevent misalignment of resources and expectations. You need to be organized and keep separate activity logs. Assign tasks and deadlines to members of your team.
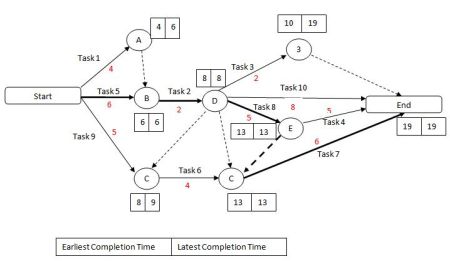
Multitasking requires more organization skills and attention to detail that managing one project. It requires communication skills as well. A strong project management program will help you avoid making mistakes and keep strong business relationships.
Goals of program management
The goals of program management include helping organizations execute their strategy, translating it into concrete goals, and minimizing risk. The program manager establishes objectives, monitors progress and communicates them with all levels of the organization. Ideally, the metrics align with the overall goals of the program. These goals help to define the project's value and purpose.
The OGC's Best Practice Guide provides guidance on program management. First, confirm the business need, secure stakeholder support, establish project management arrangements, define project scope and objectives, assess relative priorities, and then, determine what your next steps are.
The process of program management
Program management is an important part of project success. A project can provide a single service or product, while programs offer a variety of capabilities. A program's results are tangible, measurable assets that can be tracked and tested. Program management includes the allocation and control of resources.
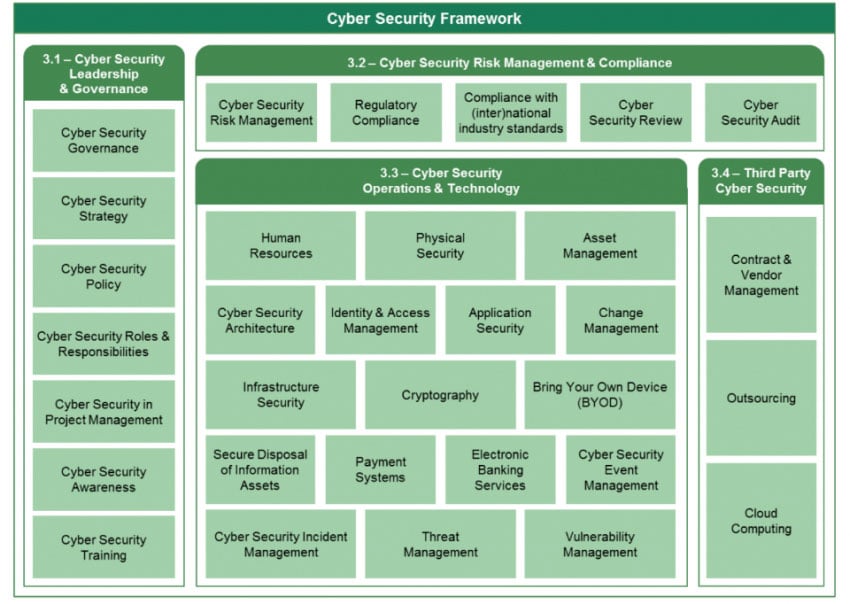
There are five stages to program management. Each stage is focused on a different aspect. Each stage requires a different set of activities to reach the desired outcome.
FAQ
What is TQM, exactly?
When manufacturing companies realized that price was not enough to compete, the industrial revolution brought about the quality movement. They had to improve efficiency and quality if they were to remain competitive.
To address this need for improvement management created Total Quality Management (TQM) which aimed to improve all aspects of an organization's performance. It included continuous improvement, employee involvement and customer satisfaction.
How can we create a successful company culture?
A company culture that values and respects its employees is a successful one.
It's based on three main principles:
-
Everybody has something of value to share
-
People are treated with respect
-
People and groups should respect each other.
These values are reflected in the way people behave. They will treat others with consideration and courtesy.
They will respect the opinions of others.
They will also encourage others to share their ideas and feelings.
In addition, the company culture encourages open communication and collaboration.
People are free to speak out without fear of reprisal.
They know that they will not be judged if they make mistakes, as long as the matter is dealt with honestly.
Finally, the company culture promotes integrity and honesty.
Everyone is aware that truth must be told.
Everyone understands that there are rules and regulations which apply to them.
Everyone does not expect to receive special treatment.
What are the steps of the management decision-making process?
Managers are faced with complex and multifaceted decisions. It involves many elements, including analysis, strategy. planning. implementation. measurement. evaluation. feedback.
Remember that people are humans just like you, and will make mistakes. This is the key to managing them. As such, there are always opportunities for improvement, especially when you put in the effort to improve yourself.
We explain in this video how the Management decision-making process works. We discuss different types of decisions as well as why they are important and how managers can navigate them. The following topics will be covered.
What is the difference between project and program?
A program is permanent while a project can be temporary.
A project typically has a defined goal and deadline.
This is often done by a group of people who report to one another.
A program typically has a set goal and objective.
It is typically done by one person.
What do we mean when we say "project management"?
This refers to managing all activities that are involved in a project's execution.
These include planning the scope and identifying the needs, creating the budget, organizing the team, scheduling the work and monitoring progress. Finally, we close down the project.
What are the five management methods?
Each business has five stages: planning, execution and monitoring.
Planning means setting goals for the long-term. This includes setting goals for the future and defining what you want.
Execution happens when you actually do the plan. It is important to ensure that everyone follows the plans.
Monitoring is the process of evaluating your progress toward achieving your objectives. Monitoring should include regular reviews of performance against goals and budgets.
Reviews take place at the end of each year. They are a chance to see if everything went smoothly during the year. If not there are changes that can be made to improve the performance next year.
Following the annual review, evaluation is done. It helps to determine what worked and what didn’t. It also provides feedback on how well people performed.
What is Six Sigma, exactly?
It is a way to improve quality that places emphasis on customer service and continuous learning. The goal is to eradicate defects through statistical techniques.
Motorola invented Six Sigma in 1986 as part its efforts to improve manufacturing.
This idea quickly spread throughout the industry. Today, many organizations use six sigma methods for product design, production and delivery.
Statistics
- Your choice in Step 5 may very likely be the same or similar to the alternative you placed at the top of your list at the end of Step 4. (umassd.edu)
- Our program is 100% engineered for your success. (online.uc.edu)
- The average salary for financial advisors in 2021 is around $60,000 per year, with the top 10% of the profession making more than $111,000 per year. (wgu.edu)
- 100% of the courses are offered online, and no campus visits are required — a big time-saver for you. (online.uc.edu)
- The BLS says that financial services jobs like banking are expected to grow 4% by 2030, about as fast as the national average. (wgu.edu)
External Links
How To
How does Lean Manufacturing work?
Lean Manufacturing methods are used to reduce waste through structured processes. They were developed in Japan by Toyota Motor Corporation (in the 1980s). The primary goal was to make products with lower costs and maintain high quality. Lean manufacturing focuses on eliminating unnecessary steps and activities from the production process. It consists of five basic elements: pull systems, continuous improvement, just-in-time, kaizen (continuous change), and 5S. It is a system that produces only the product the customer requests without additional work. Continuous improvement is the continuous improvement of existing processes. Just-in–time refers when components or materials are delivered immediately to their intended destination. Kaizen refers to continuous improvement. It is achieved through small changes that are made continuously. The 5S acronym stands for sort in order, shine standardize and maintain. These five elements are combined to give you the best possible results.
The Lean Production System
Six key concepts are the basis of lean production:
-
Flow - focus on moving material and information as close to customers as possible;
-
Value stream mapping is the ability to divide a process into smaller tasks, and then create a flowchart that shows the entire process.
-
Five S’s - Sorted, In Order. Shine. Standardize. And Sustain.
-
Kanban: Use visual signals such stickers, colored tape, or any other visual cues, to keep track your inventory.
-
Theory of constraints: Identify bottlenecks and use lean tools such as kanban boards to eliminate them.
-
Just-in-time delivery - Deliver components and materials right to your point of use.
-
Continuous improvement: Make incremental improvements to the process instead of overhauling it completely.