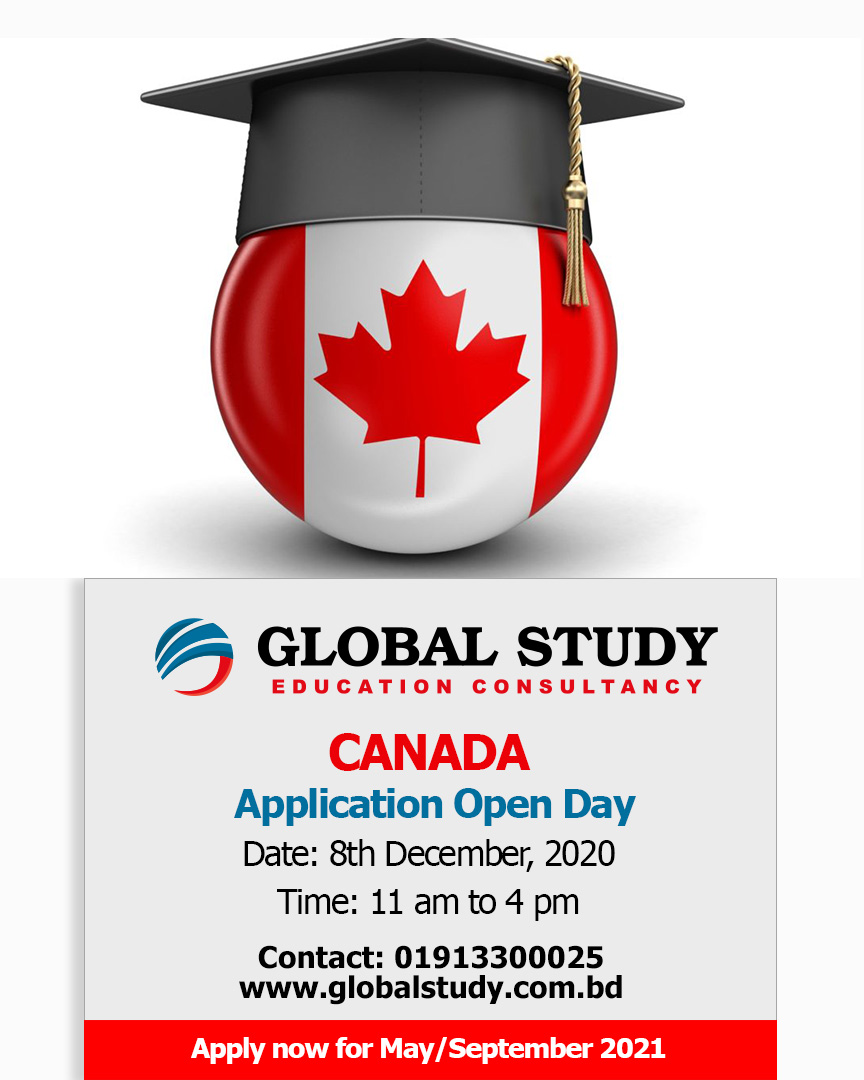
The Dynamics Supply Chain Management solution provides comprehensive functionality to manage the product lifecycle. The solution also helps companies configure items for discrete or process manufacturing, test quality of products, match items with suppliers, submit RFQs and evaluate suppliers. It offers tools to track inventory and inventories. It provides complete visibility of production and stock status. You can manage your order fulfillment from one location with this software.
Dynamics 365
Dynamics 365 Supply Chain Management's (SCM), purpose is to improve your company's operational efficiency and quality. It integrates sales, purchasing, logistics and warehouse management. It provides smart insights into every transaction. Dynamics 365 SCM can manage your distributed organization. It is also capable of handling many other tasks, including asset management, cost management master planning, product information, service management and transportation.
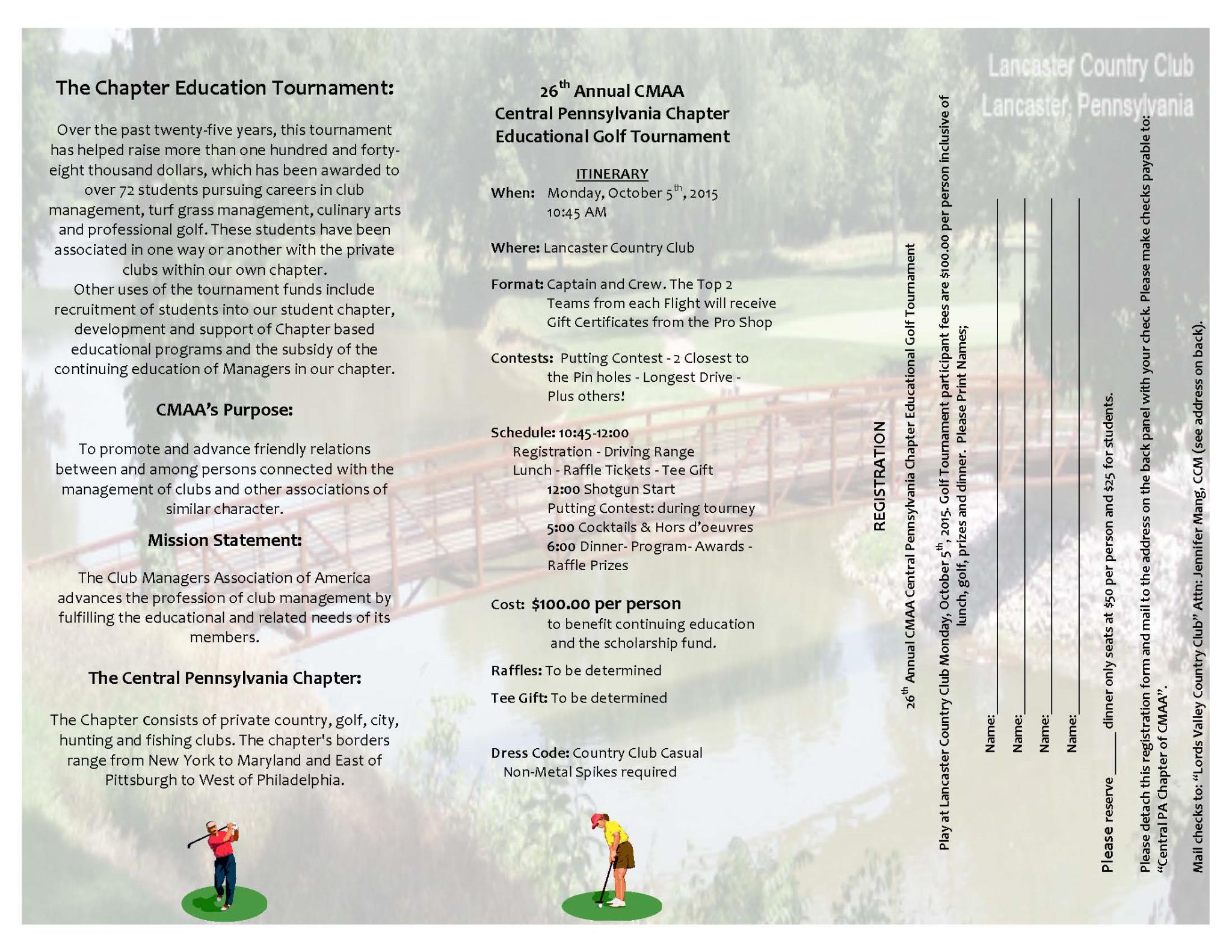
A sophisticated inventory management tool automates all steps of the manufacturing process. You can also optimize warehouse space and simplify field service operations. The software's machine-learning capabilities allow it to suggest better methods for inventory management. The software can help you achieve optimal inventory control and decrease downtime. Finally, it helps you manage the life cycle of finished goods and materials efficiently and increase the productivity of your workforce.
Dynamics 365 Planning Optimization add-in
Microsoft Dynamics 365 can help you manage your supply chain. You might be interested in the planning optimization add on. This powerful feature can help your organization plan and manage inventory, transportation, and warehouse functions. It also enables you to analyze operations using key performance indicators (KPIs). It allows inventory stock adjustments and restrictions to be made. It also automates field service operations. For more information about this powerful planning optimization add-in, read on!
Master planning is now easier with the new add-in. This add-in allows you to comply with multiple national standards in inventory accounting within one system. This add-in makes it possible to monitor inventory status at any time, from multiple sources. Inventory visibility is critical for global supply chain efficiency in this fast-changing world. This add in allows you to focus your company's manufacturing efforts on the most important tasks.
Dynamics 365 Dynamics 365 Dynamics 365 Dynamics 365 Dynamics 365 Dynamics 365 Dynamics 365 Dynamics 365 Dynamics 365 Dynamics 365 Dynamics 365 Dynamics 365 Dynamics 365 Dynamics 365 Dynamics 365 Dynamics 365 Dynamics 365 Dynamics 365 Dynamics 365 Dynamics 365 Dynamics 365 Dynamics 365 Dynamics 365 Dynamics 365 Dynamics 365 Dynamics 365 Dynamics 365 Dynamics 365 Dynamics 365 Dynamics 365 Dynamics
Microsoft Dynamics, their latest business management tool, is now available. It is the next generation for supply chain management. The new cloud-based solution incorporates all of the capabilities of the popular Dynamics AX. It can help you increase operational efficiency as well as improve the quality and performance of your product. It is possible to integrate existing systems with the software, allowing you to automate deliveries, inventory management, cost management, as well as cost management.
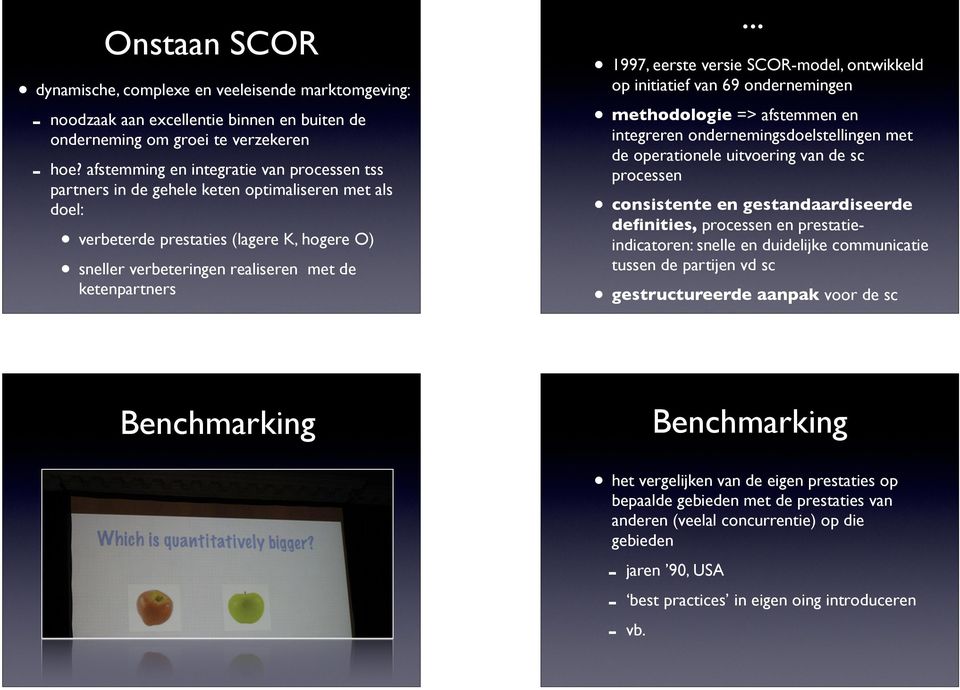
This solution integrates various functions of the supply chain into one system, including purchasing, inventory, and transportation management. It gives real-time information to enhance planning and decision-making. It supports accounting conservatism principles and offers new reporting using Power BI. It comes with a step by step setup wizard that provides near-real time visibility into inventories. Additionally, it validates fulfillment dates via an ATP Check. It allows you to allocate stock based on profitability and demand, which will allow you to make strategic business decisions that benefit your company. It automates field services, making it possible to get up and running quicker.
FAQ
What are your main management skills
Any business owner needs to be able to manage people, finances, resources and time. These skills include the ability of managing people, finances, time, space, and other factors.
These skills are necessary for setting goals and objectives as well as planning strategies, leading groups, motivating employees and solving problems.
There are so many managerial tasks!
What does Six Sigma mean?
Six Sigma uses statistical analysis to find problems, measure them, analyze root causes, correct problems, and learn from experience.
The first step to solving the problem is to identify it.
The data is then analyzed and collected to identify trends.
The problem is then rectified.
The data are then reanalyzed to see if the problem is solved.
This cycle continues until the problem is solved.
What are the five management processes?
Planning, execution, monitoring and review are the five stages of any business.
Planning is about setting goals for your future. Planning involves defining your goals and how to get there.
Execution happens when you actually do the plan. These plans must be adhered to by everyone.
Monitoring is checking on progress towards achieving your objectives. Regular reviews should be done of your performance against targets or budgets.
Reviews take place at the end of each year. They give you an opportunity to review the year and assess how it went. If not, changes may be made to improve the performance next time around.
After the annual review is complete, evaluations are conducted. It helps identify which aspects worked well and which didn't. It provides feedback about how people perform.
What role does a manager have in a company's success?
There are many roles that a manager can play in different industries.
The manager oversees the day-to-day activities of a company.
He/she is responsible for ensuring that the company meets all its financial obligations and produces the goods or services customers want.
He/she makes sure that employees adhere to the rules and regulations as well as quality standards.
He/she oversees marketing campaigns and plans new products.
What is a basic management tool used in decision-making?
A decision matrix, a simple yet powerful tool for managers to make decisions, is the best. It helps them to think strategically about all options.
A decision matrix is a way to organize alternatives into rows and columns. It is easy to see how each option affects the other options.
The boxes on the left hand side of this matrix represent four possible choices. Each box represents one option. The top row represents the current state of affairs, and the bottom row is indicative of what would happen in the event that nothing were done.
The middle column shows the effect of choosing Option 1. In this case, it would mean increasing sales from $2 million to $3 million.
The results of choosing Option 2 and 3 can be seen in the columns below. These are positive changes - they increase sales by $1 million and $500 thousand respectively. But, they also have some negative consequences. For instance, Option 2 increases cost by $100 thousand while Option 3 reduces profits by $200 thousand.
Finally, the last column shows the results of choosing Option 4. This results in a decrease of sales by $1,000,000
The best part of using a decision-matrix is that it doesn't require you to know which numbers belong where. Simply look at the cells to instantly determine if one choice is better than the other.
This is because your matrix has already done the hard work. It is as simple as comparing the numbers within the relevant cells.
Here's an example showing how you might use a Decision Matrix in your business.
You want to decide whether or not to invest more money into advertising. This will allow you to increase your revenue by $5000 per month. You'll also have additional expenses up to $10,000.
Look at the cell immediately below the one that states "Advertising" to calculate the net investment in advertising. It's $15,000. Therefore, you should choose to invest in advertising since it is worth more than the cost involved.
Statistics
- The average salary for financial advisors in 2021 is around $60,000 per year, with the top 10% of the profession making more than $111,000 per year. (wgu.edu)
- Hire the top business lawyers and save up to 60% on legal fees (upcounsel.com)
- This field is expected to grow about 7% by 2028, a bit faster than the national average for job growth. (wgu.edu)
- Your choice in Step 5 may very likely be the same or similar to the alternative you placed at the top of your list at the end of Step 4. (umassd.edu)
- The BLS says that financial services jobs like banking are expected to grow 4% by 2030, about as fast as the national average. (wgu.edu)
External Links
How To
How is Lean Manufacturing done?
Lean Manufacturing methods are used to reduce waste through structured processes. They were developed in Japan by Toyota Motor Corporation (in the 1980s). The goal was to produce quality products at lower cost. Lean manufacturing is about eliminating redundant steps and activities from the manufacturing process. It includes five main elements: pull systems (continuous improvement), continuous improvement (just-in-time), kaizen (5S), and continuous change (continuous changes). Pull systems allow customers to get exactly what they want without having to do extra work. Continuous improvement means continuously improving on existing processes. Just-in time refers to components and materials being delivered right at the place they are needed. Kaizen is continuous improvement. This can be achieved by making small, incremental changes every day. Five-S stands for sort. It is also the acronym for shine, standardize (standardize), and sustain. These five elements are combined to give you the best possible results.
Lean Production System
The lean production system is based on six key concepts:
-
Flow - The focus is on moving information and material as close as possible to customers.
-
Value stream mapping is the ability to divide a process into smaller tasks, and then create a flowchart that shows the entire process.
-
Five S's - Sort, Set In Order, Shine, Standardize, and Sustain;
-
Kanban - visual cues such as stickers or colored tape can be used to track inventory.
-
Theory of Constraints - Identify bottlenecks in the process, and eliminate them using lean tools such kanban boards.
-
Just-in-time delivery - Deliver components and materials right to your point of use.
-
Continuous improvement is making incremental improvements to your process, rather than trying to overhaul it all at once.