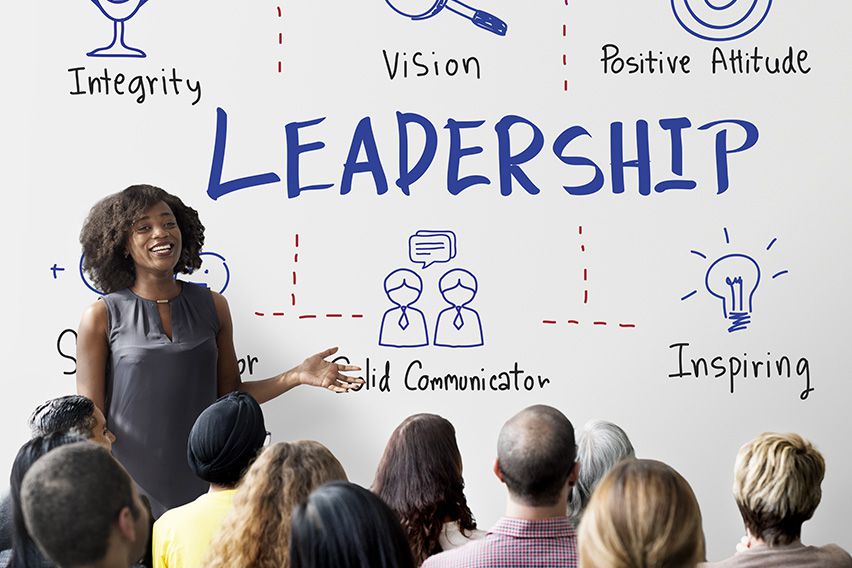
You know how important it is to reduce cycle times if you own a manufacturing company. Your cycle times will affect the speed of completing a process. Here are some ways to speed up your cycle time:
Time to process
The key manufacturing KPI is the process time cycle times. They help teams determine when to begin and finish jobs, and their overall delivery capability. The formula for calculating cycle time is simple and can be expressed as a number of units. Many manufacturing analytics software systems also include cycle time calculations. Below is an example of a cycle time breakdown:
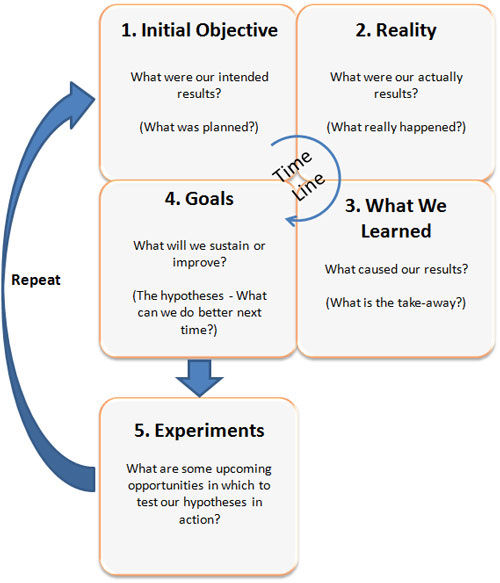
To analyze process time, the first step is to identify which steps are too slow. These steps could cause bottlenecks, which can delay the completion of other processes. In a perfect world, all process steps would work at the same speed, with no idle time or work-in-process (WIP). The process manager can measure the time taken for each step and identify areas where improvements could be made.
Order processing time
When processing an order, it is important to measure cycle times to determine how long it takes to fulfill the order. This will help you stay competitive and ahead of your competition. Calculating the cycle times is as simple as calculating how long it takes for a task to be completed, not including any waiting periods. The shipping time for the item once it's made should also be considered. If your cycle times are long, it may be time to make changes to your order processing.
Calculating cycle times is essential, regardless of whether your company processes thousands or millions orders every year. This process can help your company identify areas where you could improve processes or reduce costs. It is also useful to know how long things take so you can give your customers an accurate timeline. The cycle time formula is based on the relationship between lead time and takt time. This will give you a good idea of how long it takes for customers to get their orders.
Product production time
It is essential to optimize the production time cycle for new products and services. This will enable you to bring your product to market more quickly and save money. You can also save labor costs by reducing cycle times and improving production efficiency. Every hour that you can reduce your product cycle time, will result in less money being spent on labor, equipment, or utilities. This can increase your profits.
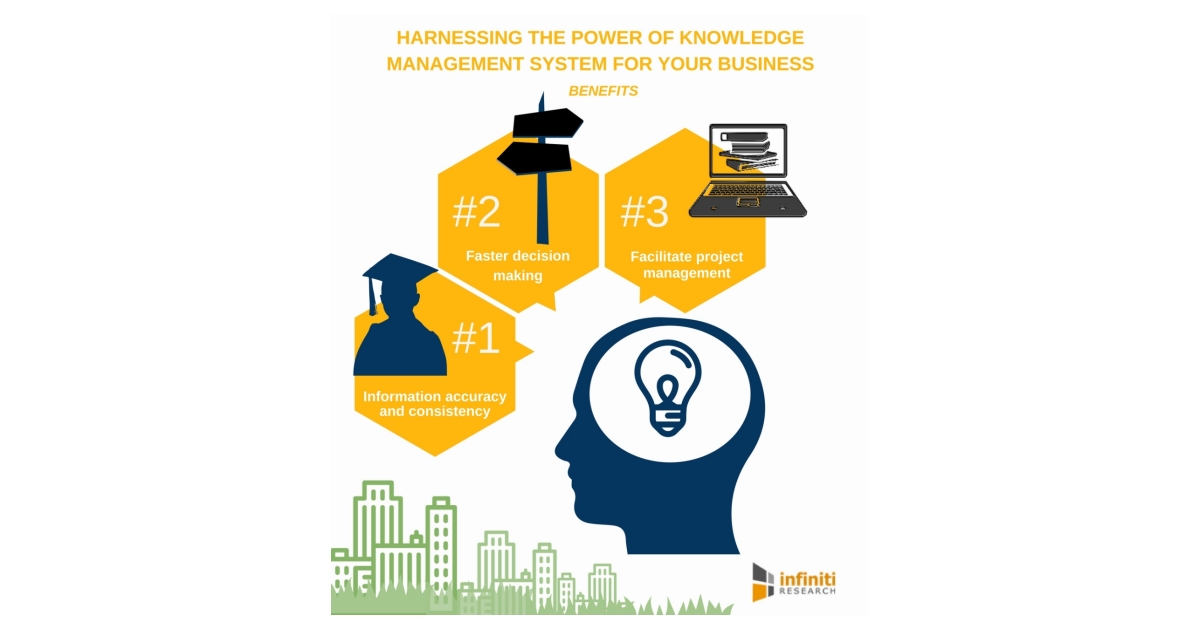
Once you have determined the costs of your product or services, you will be better able to estimate the overall cost. Once you have analyzed the cost of your product or service, you can estimate the costs for labor, materials, delivery, and shipping. This allows you to price your product according to its cost. You can use a cycle-time calculator to ensure that you are keeping your costs within acceptable limits. It can help plan ahead and make sure your project runs smoothly.
FAQ
What are the three basic management styles?
These are the three most common management styles: participative (authoritarian), laissez-faire (leavez-faire), and authoritarian. Each style has its own strengths and weaknesses. Which style do yo prefer? Why?
Autoritarian – The leader sets the direction for everyone and expects them to follow. This style is best when the organization has a large and stable workforce.
Laissez-faire - The leader allows each individual to decide for him/herself. This style works best when an organization is small and dynamic.
Participative - The leader listens to ideas and suggestions from everyone. This is a great style for smaller organizations that value everyone.
What is the meaning of "project management?"
Management is the act of managing activities in order to complete a project.
We help you define the scope of your project, identify the requirements, prepare the budget, organize the team, plan the work, monitor progress and evaluate the results before closing down the project.
What is TQM?
When manufacturing companies realized that price was not enough to compete, the industrial revolution brought about the quality movement. They had to improve efficiency and quality if they were to remain competitive.
Management realized the need to improve and created Total Quality Management, which focused on improving all aspects within an organization's performance. It included continuous improvement and employee involvement as well as customer satisfaction.
What is the difference between TQM and Six Sigma?
The main difference between these two quality management tools is that six sigma focuses on eliminating defects while total quality management (TQM) focuses on improving processes and reducing costs.
Six Sigma is an approach for continuous improvement. This method emphasizes eliminating defects using statistical methods such p-charts, control charts, and Pareto analysis.
The goal of this method is to reduce variation in product output. This is done by identifying and correcting the root causes of problems.
Total Quality Management involves monitoring and measuring every aspect of the organization. It also includes the training of employees to improve performance.
It is frequently used as an approach to increasing productivity.
Statistics
- UpCounsel accepts only the top 5 percent of lawyers on its site. (upcounsel.com)
- Your choice in Step 5 may very likely be the same or similar to the alternative you placed at the top of your list at the end of Step 4. (umassd.edu)
- This field is expected to grow about 7% by 2028, a bit faster than the national average for job growth. (wgu.edu)
- As of 2020, personal bankers or tellers make an average of $32,620 per year, according to the BLS. (wgu.edu)
- Our program is 100% engineered for your success. (online.uc.edu)
External Links
How To
How do I do the Kaizen Method?
Kaizen means continuous improvement. Kaizen is a Japanese concept that encourages constant improvement by small incremental changes. This is a collaborative process in which people work together to improve their processes continually.
Kaizen, a Lean Manufacturing method, is one of its most powerful. Kaizen is a concept where employees in charge of the production line are required to spot problems during the manufacturing process before they become major issues. This is how you can improve the quality and lower the cost.
Kaizen is the idea that every worker should be aware of what is going on around them. Correct any errors immediately to avoid future problems. Report any problem you see at work to your manager.
There are some basic principles that we follow when doing kaizen. Always start with the end product in mind and work our way back to the beginning. For example, if we want to improve our factory, we first fix the machines that produce the final product. Next, we repair the machines that make components. Then, the machines that make raw materials. We then fix the workers that work with those machines.
This method, called 'kaizen', focuses on improving each and every step of the process. Once we have finished fixing the factory, we return to the beginning and work until perfection.
You need to know how to measure the effectiveness of kaizen within your business. There are many ways you can determine if kaizen has been implemented well. One of these ways is to check the number of defects found on the finished products. Another way is to check how much productivity has grown since kaizen was implemented.
To determine if kaizen is effective, you should ask yourself why you chose to implement kaizen. Is it because the law required it or because you want to save money. Did you really think that it would help you achieve success?
Congratulations if you answered "yes" to any of the questions. You are ready to start kaizen.