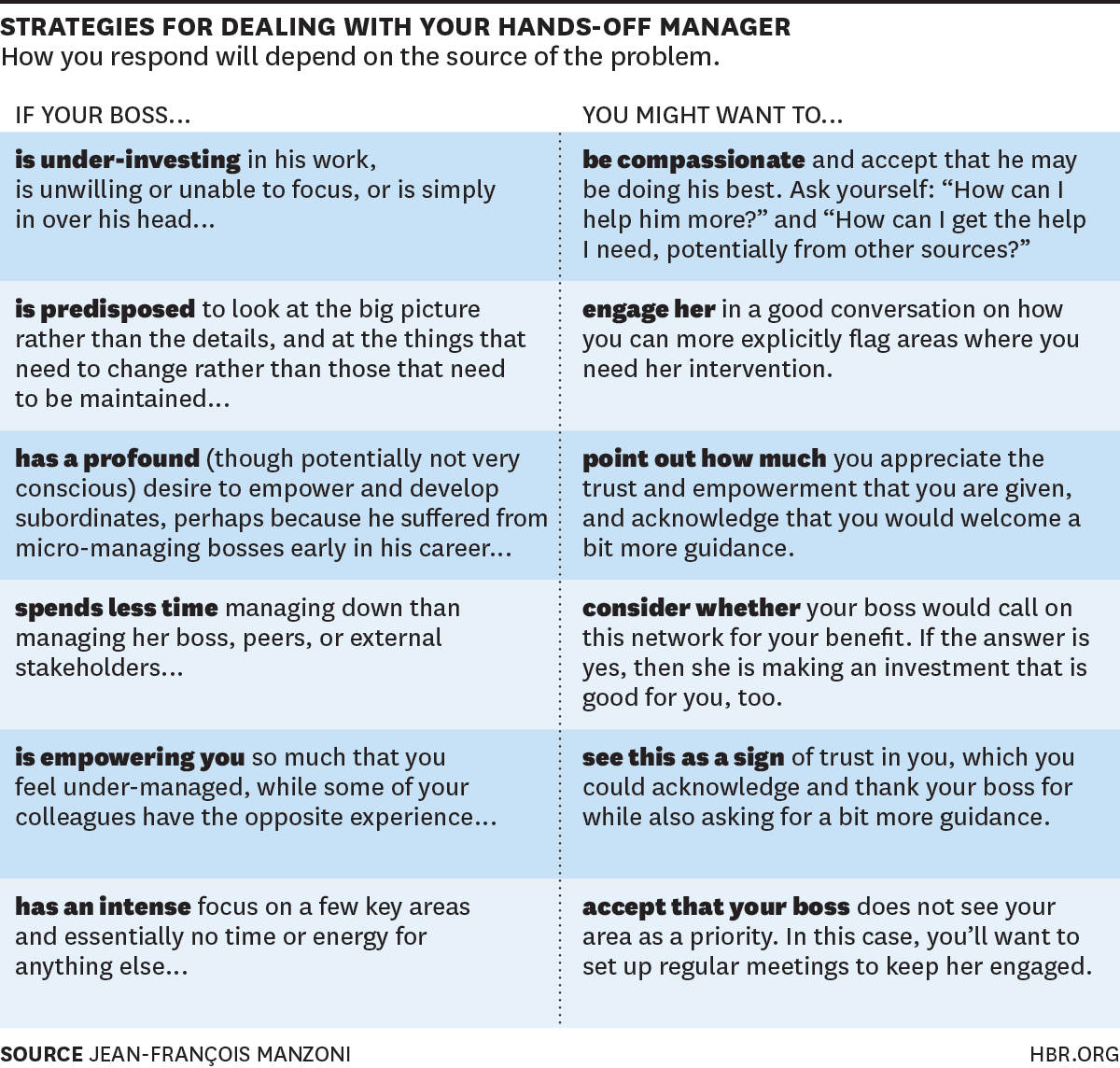
Mismanagement can be defined as the act of making a mess of what you're doing. It can include anything from spending money that isn't necessary to a breach of a contract or other legal obligation to mismanagement. Sometimes mismanagement can be caused by conflict of opinion. Here are some instances. Here are some examples.
It involves a difference between two opinions
Mismanagement can be applied to activities that are deemed wasteful. This label is often associated by grudges. As a result, there is less money available for pet project. Common examples include spending "too much" on internationalization, prioritizing a field of study over another field, or constructing a new building. However, it's important to recognize that mismanagement can also be attributed to disagreements about institutional goals.
It can be considered a breach or contract violation.
Mismanagement is a type of business practice that involves a breach of legal or contractual obligations. While most business contracts are designed to benefit all parties involved, delays, financial problems, and other unpredictable circumstances can arise that prevent a contract from being fulfilled as agreed. If this happens, the parties can sue one another for breach of contract.
FAQ
What are some common mistakes managers make?
Sometimes managers make their job harder than they need to.
They may not be able to delegate enough responsibility to staff or provide adequate support.
Additionally, many managers lack communication skills that are necessary to motivate and direct their teams.
Some managers create unrealistic expectations for their teams.
Managers may prefer to solve every problem for themselves than to delegate responsibility.
Why is it so important for companies that they use project management techniques
Project management techniques are used to ensure that projects run smoothly and meet deadlines.
Because most businesses depend heavily on project work to produce goods or services,
Companies must manage these projects effectively and efficiently.
Companies could lose their time, reputation, and money without effective project management.
It seems so difficult sometimes to make sound business decisions.
Businesses are complex systems, and they have many moving parts. People who manage them have to balance multiple priorities while dealing with complexity and uncertainty.
Understanding how these factors impact the whole system is key to making informed decisions.
It is important to consider the functions and reasons for each part of the system. It's important to also consider how they interact with each other.
You should also ask yourself if there are any hidden assumptions behind how you've been doing things. If you don't have any, it may be time to revisit them.
Asking for assistance from someone else is a good idea if you are still having trouble. You may be able to see things from a different perspective than you are and gain insight that can help you find a solution.
How does a manager motivate his/her employees?
Motivation refers to the desire to perform well.
You can get motivated by doing something enjoyable.
Or you can get motivated by seeing yourself making a contribution to the success of the organization.
For example: If you want to be a doctor, you might find it more motivating seeing patients than reading medical books all day.
Another source of motivation is within.
You might feel a strong sense for responsibility and want to help others.
You may even find it enjoyable to work hard.
If you don’t feel motivated, find out why.
You can then think of ways to improve your motivation.
What is TQM and how can it help you?
The industrial revolution was when companies realized that they couldn't compete on price alone. This is what sparked the quality movement. They had to improve efficiency and quality if they were to remain competitive.
In response to this need for improvement, management developed Total Quality Management (TQM), which focused on improving all aspects of an organization's performance. It included continual improvement processes, employee involvement, customer satisfaction, and customer satisfaction.
How does a manager develop his/her management skills?
Through demonstrating good management skills at every opportunity
Managers must monitor the performance of subordinates constantly.
If you notice your subordinate isn't performing up to par, you must take action quickly.
It is important to be able identify areas that need improvement and what can be done to improve them.
What is the difference of leadership and management?
Leadership is about being a leader. Management is about controlling others.
A leader inspires followers while a manager directs workers.
A leader motivates people and keeps them on task.
A leader develops people; a manager manages people.
Statistics
- As of 2020, personal bankers or tellers make an average of $32,620 per year, according to the BLS. (wgu.edu)
- The profession is expected to grow 7% by 2028, a bit faster than the national average. (wgu.edu)
- The average salary for financial advisors in 2021 is around $60,000 per year, with the top 10% of the profession making more than $111,000 per year. (wgu.edu)
- This field is expected to grow about 7% by 2028, a bit faster than the national average for job growth. (wgu.edu)
- UpCounsel accepts only the top 5 percent of lawyers on its site. (upcounsel.com)
External Links
How To
How can you implement the Kaizen technique?
Kaizen means continuous improvement. The Japanese philosophy emphasizes small, incremental improvements to achieve continuous improvement. This term was created by Toyota Motor Corporation in 1950. It's a team effort to continuously improve processes.
Kaizen is one the most important methods of Lean Manufacturing. Employees responsible for the production line should identify potential problems in the manufacturing process and work together to resolve them. This will increase the quality and decrease the cost of the products.
Kaizen is the idea that every worker should be aware of what is going on around them. If something is wrong, it should be corrected immediately so that no problem occurs. Report any problem you see at work to your manager.
There are some basic principles that we follow when doing kaizen. We always start from the end product and move toward the beginning. If we want to improve our factory for example, we start by fixing the machines that make the final product. Then, we fix the machines that produce components and then the ones that produce raw materials. And finally, we fix the workers who work directly with those machines.
This approach is called 'kaizen' because it focuses on improving everything steps by step. After we're done with the factory, it's time to go back and fix the problem.
How to measure kaizen's effectiveness in your business is essential to implement it. There are many ways you can determine if kaizen has been implemented well. One method is to inspect the finished products for defects. Another way is to see how much productivity has increased since implementing kaizen.
You can also find out if kaizen works by asking yourself why you decided to implement it. You were trying to save money or obey the law? Did you really think that it would help you achieve success?
Suppose you answered yes to any of these questions, congratulations! You're now ready to get started with kaizen.