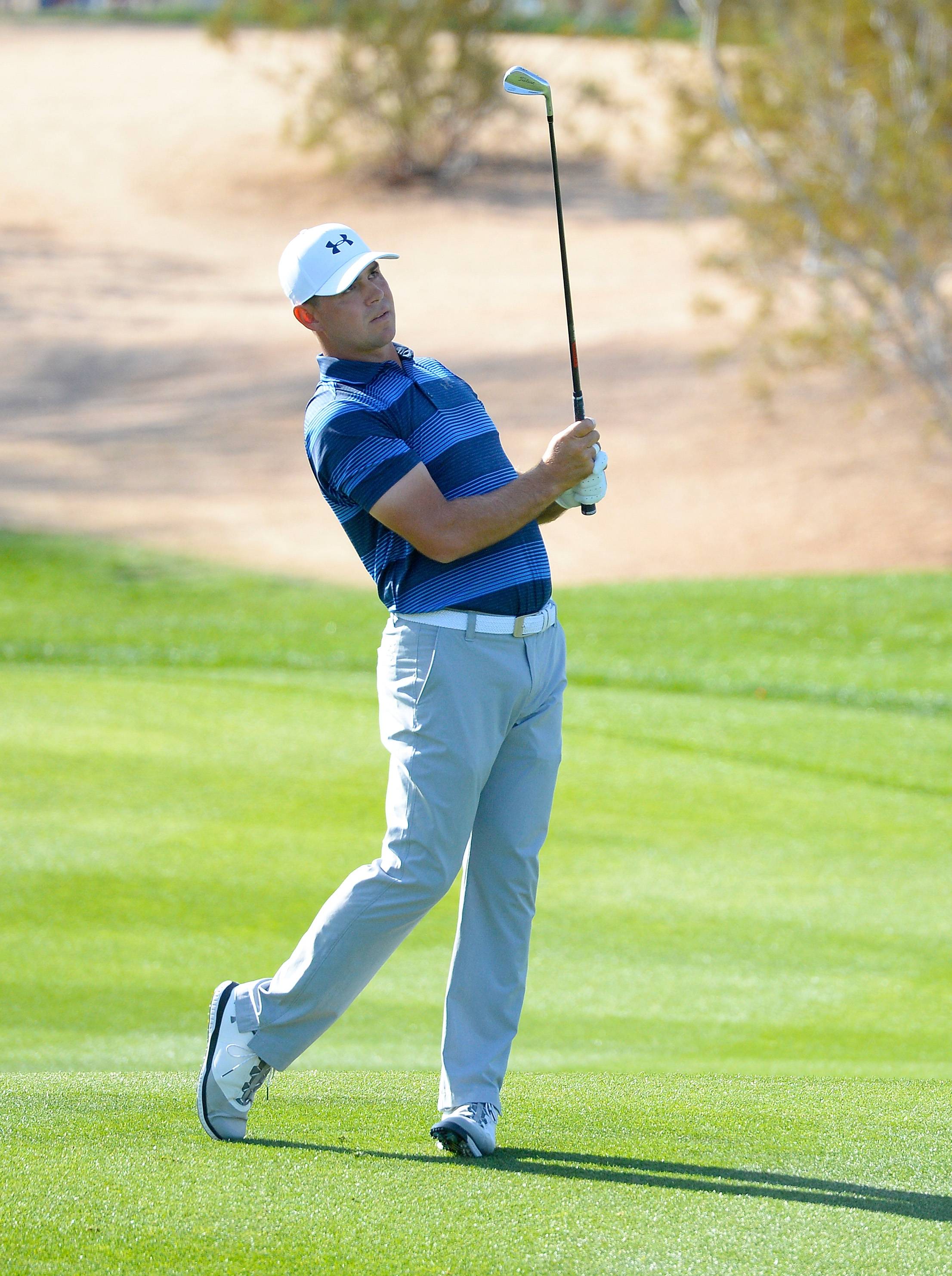
This book will provide you with a practical and strategic strategy for managing global supply chains. This book offers both practitioners and researchers a well-organized, detailed and understandable content. This book is highly recommendable. This book explains key concepts and the processes involved in strategic supply chain management. The authors provide a step by step guide to achieving strategic supply chains objectives. It is highly recommended to both practitioners as well as researchers.
Demand-driven supply chain
A demand-driven Supply Chain is a strategic supply system in which all the chains respond to changes of demand. In this way, companies are able to anticipate and fulfill customer requests in real time. It is different to the traditional model, in which the supplier announces new products and the retailer delivers them. This model helps companies increase efficiency and keep their inventory under control. This allows companies to respond to customer demand faster and more efficiently through demand-driven supply chain.
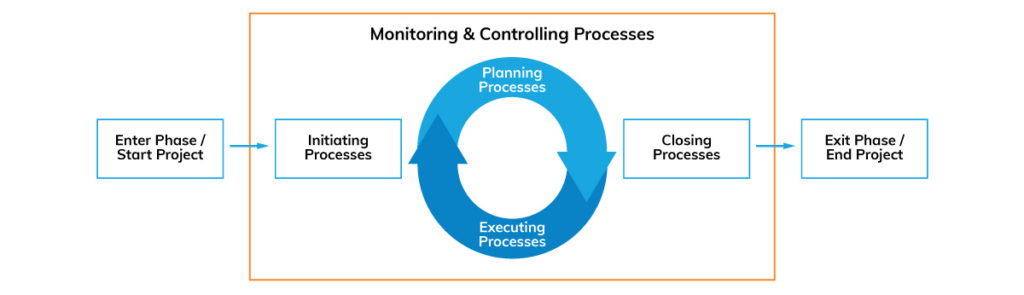
Plan
To optimize and plan the supply chain, tools that are organization-based are used. These planning approaches support different types of decision-making. An annual strategic business plan is essential to ensure a company's success and to identify growth opportunities. Many organizations use supply chain management software to optimize and plan their supply chains. Here are some examples of different planning approaches. You can pick one depending on which type of planning you prefer.
Execution
Strategic supply chain management is the formal approach to managing the supply chain network of an organization. A supply chain manager creates a strategy that maximizes value, efficiency, resilience. It must align with the company's overarching business strategy. Successful supply chain management requires careful planning and execution. It is important to fully understand the role of your supply chain in your business strategy. Here are some ways to manage your supply chain effectively. Start by creating a strategic vision to guide your supply chain.
Monitoring
Effective management depends on information. Managers will not make the best decisions if they don't have the data or tools to take corrective action. As supply chains become more complex, managers who fail to monitor the process can't be prepared for potential disruptions or hazards. Supply chain monitoring has become a must. Monitoring your supply chain has many benefits. Here are a few. You can read on to learn more.
Sustainability
It is not easy to achieve sustainability in a strategic supplier chain. It is more challenging to achieve true sustainability in a strategic supply chain that is more complicated. Therefore, the procurement group should designate someone to manage the sustainability process. They also need to regularly evaluate the progress made by suppliers. The procurement team should also set specific sustainability goals and require the suppliers to meet these goals. The whole process will become transparent. An excellent way to assess supplier performance is to count the number products or services that are in line with the company's sustainability objectives.
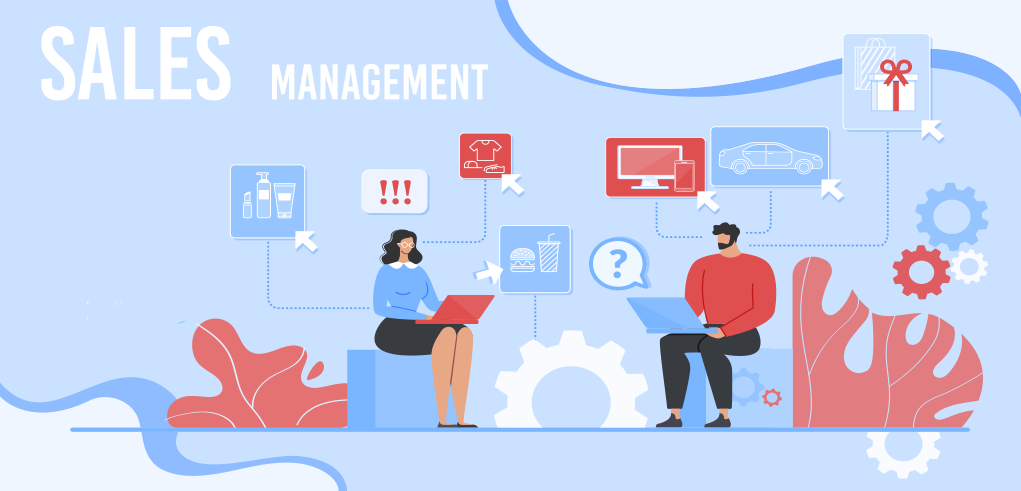
Variations based on product type
To achieve optimal performance, companies need to offer a wide variety of products to their consumers. They often introduce product variations without realizing if they will cause additional complexity in their supply chains. For example, from 2002 to 2011, consumer-goods companies increased the number of new products they launched each year by 60 percent. While this influx increased demand, it also raised costs throughout their supply chains. The U.S. consumer products companies also increased the number and quality of new products that they introduce each year by 60 percent over the same period. While this undoubtedly pushed up the costs of many areas in the company's supply chains, it did so at a steady rate only 2.8% per year.
FAQ
What is the difference in Six Sigma and TQM?
The main difference in these two quality management tools lies in the fact that six sigma is focused on eliminating defects and total quality management (TQM), emphasizes improving processes and reducing costs.
Six Sigma can be described as a strategy for continuous improvement. It emphasizes the elimination and improvement of defects using statistical methods, such as control charts, P-charts and Pareto analysis.
This method attempts to reduce variations in product output. This is achieved by identifying and addressing the root causes of problems.
Total Quality Management involves monitoring and measuring every aspect of the organization. Training employees is also part of total quality management.
It is commonly used as a strategy for increasing productivity.
Why is it so important for companies that they use project management techniques
Project management techniques are used in order to ensure projects run smoothly, and that deadlines are met.
This is due to the fact that most businesses rely heavily upon project work in order to produce goods, and services.
Companies need to manage these projects efficiently and effectively.
Companies that do not manage their projects effectively risk losing time, money, or reputation.
How do we build a culture that is successful in our company?
A successful company culture is one that makes people feel valued and respected.
It is founded on three basic principles:
-
Everyone has something to contribute
-
Fair treatment of people is the goal
-
Respect is shared between individuals and groups
These values reflect in how people behave. They will treat others with consideration and courtesy.
They will respect the opinions of others.
They can also be a source of inspiration for others.
In addition, the company culture encourages open communication and collaboration.
People feel free to express their views openly without fear of reprisal.
They understand that mistakes can be forgiven as long as they're dealt with honestly.
The company culture encourages honesty and integrity.
Everyone understands that the truth is always best.
Everyone is aware that rules and regulations apply to them.
And no one expects special treatment or favors.
What is a basic management tool that can be used for decision-making?
A decision matrix is an easy but powerful tool to aid managers in making informed decisions. It helps them to think strategically about all options.
A decision matrix can be used to show alternative options as rows or columns. This allows you to easily see how each choice affects others.
We have four options in this example. They are represented by the boxes to the left of the matrix. Each box represents a different option. The top row shows the status quo (the current situation), and the bottom row shows what would happen if nothing was done at all.
The middle column shows the effect of choosing Option 1. This would result in an increase of sales of $2 million to $3million.
The results of choosing Option 2 and 3 can be seen in the columns below. These are positive changes - they increase sales by $1 million and $500 thousand respectively. But, they also have some negative consequences. Option 2 increases costs by $100 thousand, while Option 3 decreases profits to $200 thousand.
Finally, the last column shows the results of choosing Option 4. This would result in a reduction of sales of $1 million.
The best thing about using a decision matrix is that you don't need to remember which numbers go where. You can just glance at the cells and see immediately if one given choice is better.
The matrix already does all the work. It's as easy as comparing numbers in the appropriate cells.
Here is an example how you might use the decision matrix in your company.
You need to decide whether to invest in advertising. You'll be able increase your monthly revenue by $5000 if you do. However, this will mean that you'll have additional expenses of $10,000.
If you look at the cell that says "Advertising", you can see the number $15,000. Advertising is a worthwhile investment because it has a higher return than the costs.
Statistics
- Hire the top business lawyers and save up to 60% on legal fees (upcounsel.com)
- As of 2020, personal bankers or tellers make an average of $32,620 per year, according to the BLS. (wgu.edu)
- The average salary for financial advisors in 2021 is around $60,000 per year, with the top 10% of the profession making more than $111,000 per year. (wgu.edu)
- Your choice in Step 5 may very likely be the same or similar to the alternative you placed at the top of your list at the end of Step 4. (umassd.edu)
- The BLS says that financial services jobs like banking are expected to grow 4% by 2030, about as fast as the national average. (wgu.edu)
External Links
How To
How does Lean Manufacturing work?
Lean Manufacturing processes are used to reduce waste and improve efficiency through structured methods. They were developed by Toyota Motor Corporation in Japan during the 1980s. The main goal was to produce products at lower costs while maintaining quality. Lean manufacturing is about eliminating redundant steps and activities from the manufacturing process. It has five components: continuous improvement and pull systems; just-in time; continuous change; and kaizen (continuous innovation). It is a system that produces only the product the customer requests without additional work. Continuous improvement involves constantly improving upon existing processes. Just-in-time is when components and other materials are delivered at their destination in a timely manner. Kaizen is continuous improvement. This can be achieved by making small, incremental changes every day. Last but not least, 5S is for sort. To achieve the best results, these five elements must be used together.
Lean Production System
Six key concepts make up the lean manufacturing system.
-
Flow - The focus is on moving information and material as close as possible to customers.
-
Value stream mapping - break down each stage of a process into discrete tasks and create a flowchart of the entire process;
-
Five S's: Sort, Shine Standardize, Sustain, Set In Order, Shine and Shine
-
Kanban - use visual signals such as colored tape, stickers, or other visual cues to keep track of inventory;
-
Theory of constraints: Identify bottlenecks and use lean tools such as kanban boards to eliminate them.
-
Just-in time - Get components and materials delivered right at the point of usage;
-
Continuous improvement: Make incremental improvements to the process instead of overhauling it completely.