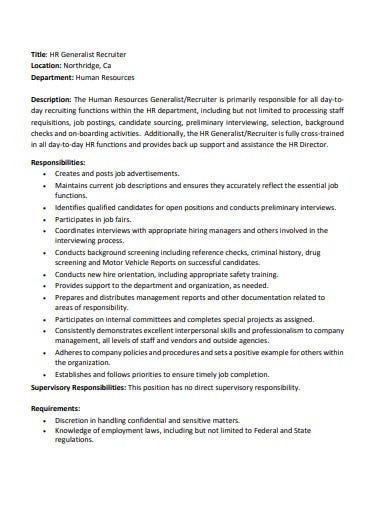
Management of supply chain risk can involve many different types of risks. These risks may be related to the supply or demand for a product. Demand risks can occur when a business underestimates demand for a product. While supply risks can arise when raw material do not arrive on a timely basis. Both these risks can disrupt the flow of product. There are also environmental risks in the supply chain that can be caused by social, political and environmental issues.
Cybersecurity is a critical component of supply chain risk and management
Supply chain risk management is about cybersecurity measures to avoid cyber attacks on critical assets. These measures could include the development of a cybersecurity strategy and the establishment of supplier controls. A contract should be drawn up by companies to detail their security requirements. These contracts should describe what they are expected do to protect assets. If a supplier fails to meet these standards, the company should consider escrow services to ensure that sensitive information is not misused.
Cyber threats will become increasingly complex as supply chains become more complex. This means that it is essential to carefully assess and mitigate these risks. Cyber threats can happen at any stage of the supply chain. Their impact on a company’s financial, brand and operational health can be catastrophic. Therefore, cybersecurity must be addressed at all stages of the supply chain.
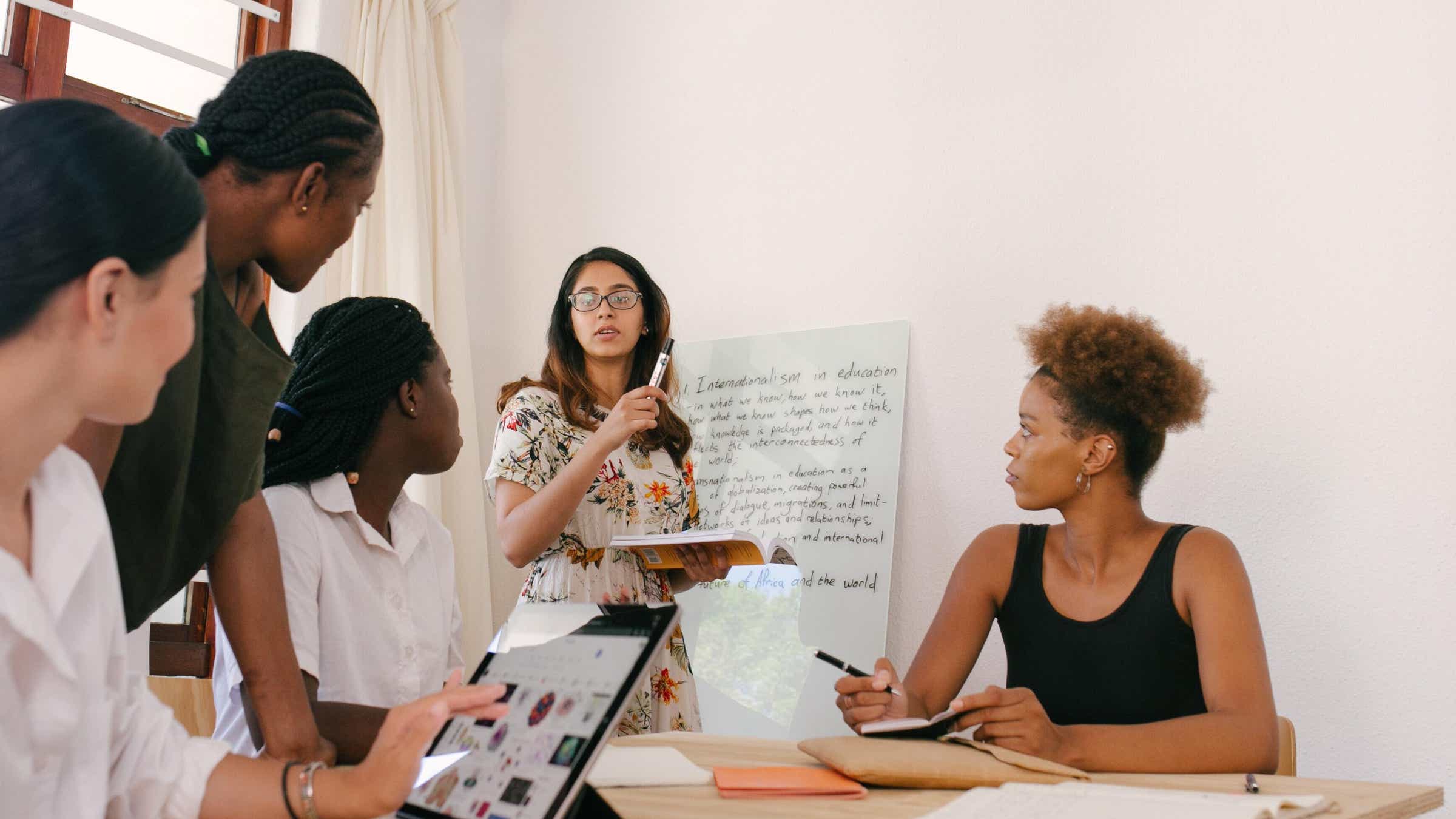
It requires a crossfunctional team
To manage supply chain risks, a cross-functional team must be formed to oversee the whole supply chain. This strategy should include preparation, response, and recovery. Preparation means identifying high risk areas and creating contingency planning to address them. Prioritizing risks according severity and likelihood should be part of the plan. Visibility is another important aspect of a supply chain management strategy.
Executives have been slow to address the issue of supply chain risk management despite its importance. In a survey of 639 executives, spanning multiple industries and regions, 71 percent of respondents said their companies were more exposed to supply chain disruption than they were two years ago and 72 percent expected the risks to continue to grow. The government has established several agencies to deal with supply chain risk. However, the private sector still needs a proven method that can minimize disruption.
Effective supply chain boards review the top risks in the supply chain and identify mitigation actions. Each participant takes responsibility for the mitigation action after the review. For example, a procurement representative is responsible for defining a new supplier's qualification and onboarding.
It requires technology
Companies are changing their approach to managing supply chain risk as they seek to lower costs and improve resilience. Technology is helping them to gain greater visibility and prevent potential risks from arising. The right technology will help companies build stronger global networks as well as resilient supply chains. To fully reap the benefits of technology, businesses need access to accurate data and visibility platforms. They will have to manage supply chain risk on a reactive basis without these data and visibility platforms.
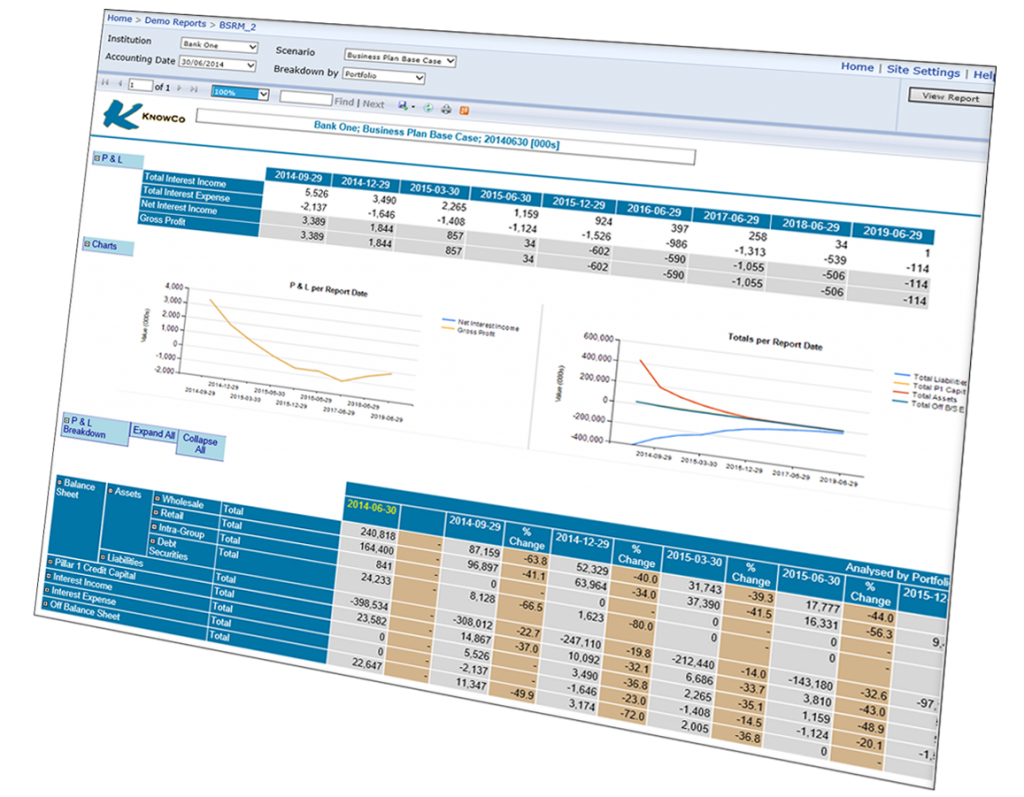
Supply chain risk management can be complex and multifaceted. A recent survey of 639 industry leaders found that 71% thought their supply chain was more vulnerable than it used to be and that the risk would increase. The United States government established a variety of agencies to address supply chains risk. One of these agencies is the Protecting Critical Technology Task Force, which is part of the Department of Defense. Private companies are also looking for proven methods to reduce the negative impact of supply chain risk on their businesses.
FAQ
Why does it sometimes seem so hard to make good business decisions
Complex systems are often complex and have many moving parts. People who manage them have to balance multiple priorities while dealing with complexity and uncertainty.
The key to making good decisions is to understand how these factors affect the system as a whole.
You need to be clear about the roles and responsibilities of each system. It is important to then consider how the individual pieces relate to each other.
Also, you should ask yourself if there have been any assumptions in your past behavior. If not, you might want to revisit them.
Asking for assistance from someone else is a good idea if you are still having trouble. They might see things differently than you and may have some insights that could help find a solution.
What are management concepts, you ask?
Management concepts are the fundamental principles and practices that managers use when managing people and their resources. These include topics such as human resource policies and job descriptions, performance assessments, training programs and employee motivation.
What is the difference between TQM and Six Sigma?
The major difference between the two tools for quality management is that six Sigma focuses on eliminating defect while total quality control (TQM), on improving processes and decreasing costs.
Six Sigma can be described as a strategy for continuous improvement. This method emphasizes eliminating defects using statistical methods such p-charts, control charts, and Pareto analysis.
This method attempts to reduce variations in product output. This is accomplished through identifying and correcting root causes.
Total quality management refers to the monitoring and measurement of all aspects in an organization. It also includes training employees to improve performance.
It is often used as a strategy to increase productivity.
What are the most important management skills?
Management skills are essential for any business owner, whether they're running a small local store or an international corporation. These skills include the ability of managing people, finances, time, space, and other factors.
These skills are necessary for setting goals and objectives as well as planning strategies, leading groups, motivating employees and solving problems.
You can see that there are many managerial duties.
Why is it important that companies use project management methods?
Project management techniques can be used to ensure smooth project execution and meeting deadlines.
This is due to the fact that most businesses rely heavily upon project work in order to produce goods, and services.
These projects require companies to be efficient and effective managers.
Without effective project management, companies may lose money, time, and reputation.
Statistics
- Hire the top business lawyers and save up to 60% on legal fees (upcounsel.com)
- The BLS says that financial services jobs like banking are expected to grow 4% by 2030, about as fast as the national average. (wgu.edu)
- Your choice in Step 5 may very likely be the same or similar to the alternative you placed at the top of your list at the end of Step 4. (umassd.edu)
- This field is expected to grow about 7% by 2028, a bit faster than the national average for job growth. (wgu.edu)
- UpCounsel accepts only the top 5 percent of lawyers on its site. (upcounsel.com)
External Links
How To
What is Lean Manufacturing?
Lean Manufacturing techniques are used to reduce waste while increasing efficiency by using structured methods. They were created in Japan by Toyota Motor Corporation during the 1980s. It was designed to produce high-quality products at lower prices while maintaining their quality. Lean manufacturing is about eliminating redundant steps and activities from the manufacturing process. It consists of five basic elements: pull systems, continuous improvement, just-in-time, kaizen (continuous change), and 5S. It is a system that produces only the product the customer requests without additional work. Continuous improvement is constantly improving upon existing processes. Just-in-time refers to when components and materials are delivered directly to the point where they are needed. Kaizen means continuous improvement, which is achieved by implementing small changes continuously. Finally, 5S stands for sort, set in order, shine, standardize, and sustain. These five elements are used together to ensure the best possible results.
The Lean Production System
Six key concepts form the foundation of the lean production system:
-
Flow - focuses on moving information and materials as close to customers as possible.
-
Value stream mapping - break down each stage of a process into discrete tasks and create a flowchart of the entire process;
-
Five S's – Sort, Put In Order Shine, Standardize and Sustain
-
Kanban: Use visual signals such stickers, colored tape, or any other visual cues, to keep track your inventory.
-
Theory of constraints - identify bottlenecks during the process and eliminate them with lean tools like Kanban boards.
-
Just-in-time - deliver components and materials directly to the point of use;
-
Continuous improvement - incremental improvements are made to the process, not a complete overhaul.