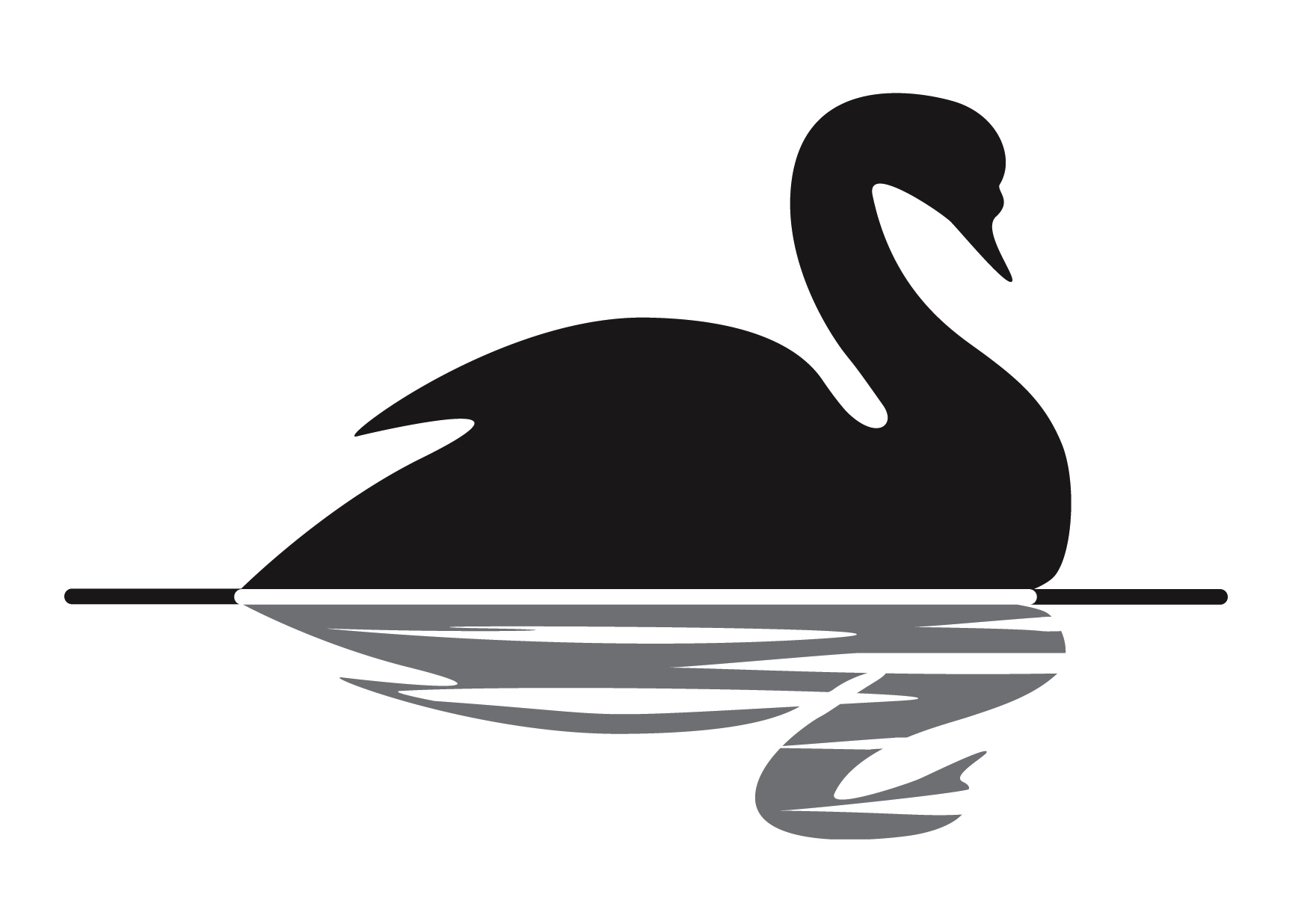
A business flow measurement does not take into account the inherent directionality, or even directionality, of supply networks. A supply network is often composed of many levels and dependencies. In addition, a business flow metric fails to capture the inherent directionality of information flows within a network. Understanding and considering these issues is key to the creation of a digital supply net.
Sustainability
Multinational corporations should consider sustainability in their supply network management strategies. Many corporations have made sustainability a top priority and have committed to using sustainable vendors. But, many suppliers below the management level do not adhere to sustainability standards. This poses serious risks for businesses. This article examines three major MNCs' supply networks. The authors found some best practices that companies could adopt to counter this problem. These include setting long-term sustainability goals and including lower-tier suppliers in the sustainability strategy.
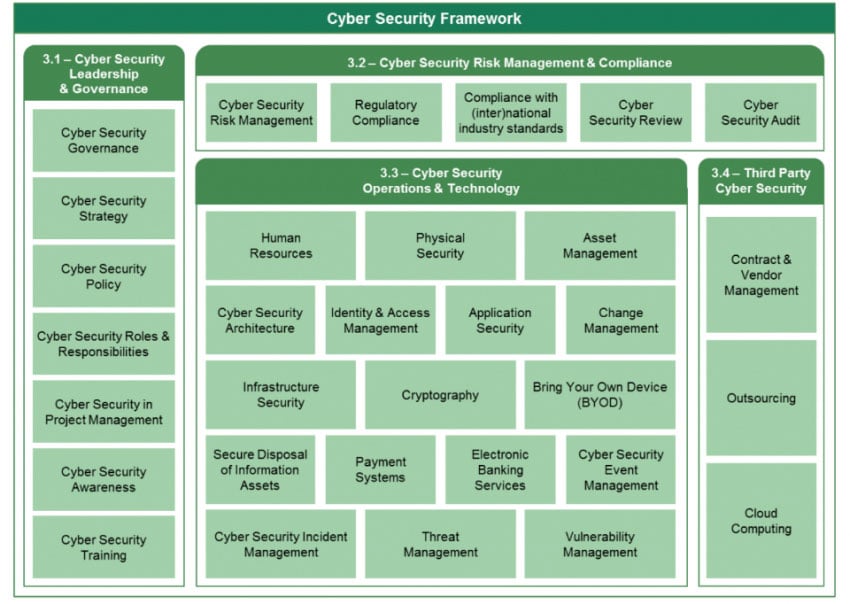
To demonstrate their improvement in supply chain management, companies must set goals and track progress. They should engage all stakeholders within the supply chain, from internal staff driving change to consumers. The goal should not be to prove the benefits to business of sustainable supply networks but to create the governance and organizational structures necessary to ensure that the sustainability efforts are a success.
Vertical disintegration of supply chains
For firms, vertical disintegration of supply chain can have many negative consequences. This can result in higher costs and losses and may also cause changes to organisational structures and hierarchies. To increase their overall competitiveness and reduce their participation in upstream or downstream activities, some companies may consider this option. This is not always an appropriate approach and should only ever be applied in particular circumstances.
Vertical integration has one major drawback: it restricts a company’s flexibility. Vertical integration forces a company to follow the trends in a specific segment. For example, it may be difficult for a retailer to adopt a new technology because its competition has already adopted it. If this was the case, the parent would have to invest money in the new technology to keep pace with the competition. Integration can also be complicated due to rapid technological changes. It can also be expensive for companies to integrate different technologies in different parts of their supply chain.
Performance implications of digital supply networks
Digital supply chains can have many benefits. They are more efficient, resilient, and cost-savings. They can also pose cybersecurity risks. These risks can be mitigated by a variety of approaches that companies can take. Let's look at some. These methods use data analytics. This technology allows businesses to understand customer expectations and can improve their products or services. Companies can use the shared data to predict potential problems and make more informed decisions by incorporating information from multiple sources.
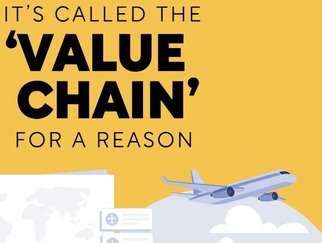
Your existing supply chain should be assessed before you can implement digitalization. This will allow for you to assess your existing supply chain and identify any potential issues. You can then create an action plan to reduce any potential risks. Once you have a clear idea of the goals you want to achieve through the digital supply network, collaboration with your partners is essential. This way, you can ensure that the new digital supply chain will meet the needs of all stakeholders.
FAQ
How can a manager improve his/her managerial skills?
By practicing good management skills at all times.
Managers need to monitor their subordinates' performance.
You must act quickly if you notice that your subordinate isn’t performing to their standards.
You should be able pinpoint what needs to improve and how to fix it.
What are management concepts?
Management concepts are the practices and principles managers use to manage people or resources. These include topics such as human resource policies and job descriptions, performance assessments, training programs and employee motivation.
What role should a manager play within a company
Each industry has a different role for a manager.
A manager generally manages the day to-day operations in a company.
He/she will ensure that the company fulfills its financial obligations.
He/she ensures that employees follow the rules and regulations and adhere to quality standards.
He/she plans and oversees marketing campaigns.
What are the three main management styles you can use?
These are the three most common management styles: participative (authoritarian), laissez-faire (leavez-faire), and authoritarian. Each style is unique and has its strengths as well as weaknesses. Which style do you prefer? Why?
Authority - The leader is the one who sets the direction and expects everyone in the organization to follow it. This style is most effective when an organization is large, stable, and well-run.
Laissez-faire: The leader lets each person decide for themselves. This style is best when the organization has a small but dynamic group.
Participative - The leader listens to ideas and suggestions from everyone. This style is most effective in smaller organizations, where everyone feels valued.
What is the difference in Six Sigma and TQM?
The major difference between the two tools for quality management is that six Sigma focuses on eliminating defect while total quality control (TQM), on improving processes and decreasing costs.
Six Sigma is an approach for continuous improvement. It emphasizes the elimination or minimization of defects through statistical methods such control charts and p charts.
This method seeks to decrease variation in product output. This is accomplished through identifying and correcting root causes.
Total quality management includes monitoring and measuring all aspects of an organization's performance. It also includes training employees to improve performance.
It is frequently used as an approach to increasing productivity.
What kind people use Six Sigma?
People who have worked with statistics and operations research will usually be familiar with the concepts behind six sigma. However, anyone involved in any aspect of business can benefit from using it.
It is a commitment-intensive task that requires strong leadership skills.
What is Six Sigma?
Six Sigma uses statistical analyses to locate problems, measure them, analyze root cause, fix problems and learn from the experience.
The first step to solving the problem is to identify it.
Next, data will be collected and analyzed to determine trends and patterns.
Next, corrective steps are taken to fix the problem.
Finally, data is reanalyzed to determine whether the problem has been eliminated.
This cycle will continue until the problem is solved.
Statistics
- The average salary for financial advisors in 2021 is around $60,000 per year, with the top 10% of the profession making more than $111,000 per year. (wgu.edu)
- Your choice in Step 5 may very likely be the same or similar to the alternative you placed at the top of your list at the end of Step 4. (umassd.edu)
- Hire the top business lawyers and save up to 60% on legal fees (upcounsel.com)
- As of 2020, personal bankers or tellers make an average of $32,620 per year, according to the BLS. (wgu.edu)
- The BLS says that financial services jobs like banking are expected to grow 4% by 2030, about as fast as the national average. (wgu.edu)
External Links
How To
How can you implement the Kaizen technique?
Kaizen means continuous improvement. The term was coined in the 1950s at Toyota Motor Corporation and refers to the Japanese philosophy emphasizing constant improvement through small incremental changes. It's a team effort to continuously improve processes.
Kaizen is one method that Lean Manufacturing uses to its greatest advantage. Kaizen is a concept where employees in charge of the production line are required to spot problems during the manufacturing process before they become major issues. This way, the quality of products increases, and the cost decreases.
Kaizen is about making everyone aware of the world around them. So that there is no problem, you should immediately correct it if something goes wrong. If someone spots a problem while at work, they should immediately report it to their manager.
Kaizen has a set of basic principles that we all follow. Always start with the end product in mind and work our way back to the beginning. To improve our factory, for example, we need to fix the machines that produce the final product. Next, we fix the machines which produce components. And finally, we fix the workers who work directly with those machines.
This is known as "kaizen", because it emphasizes improving each step. Once the factory is fixed, we return to the original site and work our way back until we get there.
You need to know how to measure the effectiveness of kaizen within your business. There are many methods to assess if kaizen works well. One method is to inspect the finished products for defects. Another way is to check how much productivity has grown since kaizen was implemented.
A good way to determine whether kaizen has been implemented is to ask why. Is it because the law required it or because you want to save money. You really believed it would make you successful?
Congratulations if you answered "yes" to any of the questions. You're ready to start kaizen.