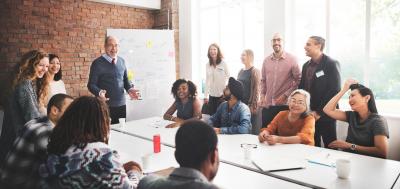
If you haven't heard of management of change (MOC), then you should. This best practice can help you avoid unwanted consequences and keep your company running smoothly. More information about MOC (and its stages) can be found below. Here are eight essential MOC stages. If you can follow these stages, it will be easy to manage any change within your organization. So what exactly is MOC, you ask? It is important to understand why it matters.
MOC is a process
MOC is often overlooked by organizations. The lack of process safety information and unfamiliarity are the main causes of workplace accidents. Organizations are quick to change in an effort to get the job done. They neglect the importance and need for risk management. Unless they're in the process of redesigning their production processes, changes to existing systems and procedures can result in accidents. This is especially true for industries dealing with energy and hazardous substances.

It consists in eight stages
McKinsey’s Change Management Model describes the change process in eight stages. These include preparation, implementation and monitoring. Evaluation, evaluation, sustainability. The first three stages of the change process focus on business, while the final two address emotional aspects. Culture must be considered in the eighth stage. In order to embrace new practices within the existing work culture, it is necessary to consider culture. To ensure that successful change management is possible, the organization's culture should be able adapt to the changes.
It prevents unintended consequences
Unintended consequences can occur when people don't always consider the consequences of their actions before they make a decision. People might decide to base their decisions on past performance and not the current situation. Unintended consequences can have disastrous effects and ultimately lead to counterproductive decisions. There are methods to manage change and reduce unintended consequences. A new process may have both positive and negative unintended consequences. For example, if a new technology is introduced, a test group will be established to assess its impact.
It is a great practice
Management of change is a key factor in ensuring a better future. This best practice is able to facilitate organizational changes. It can be applied from identifying the vision to engaging your team. It is important that you remember that change management involves many soft elements. These are key to the success of any management change effort. These elements must be taken into account in order to make the whole change process smooth.
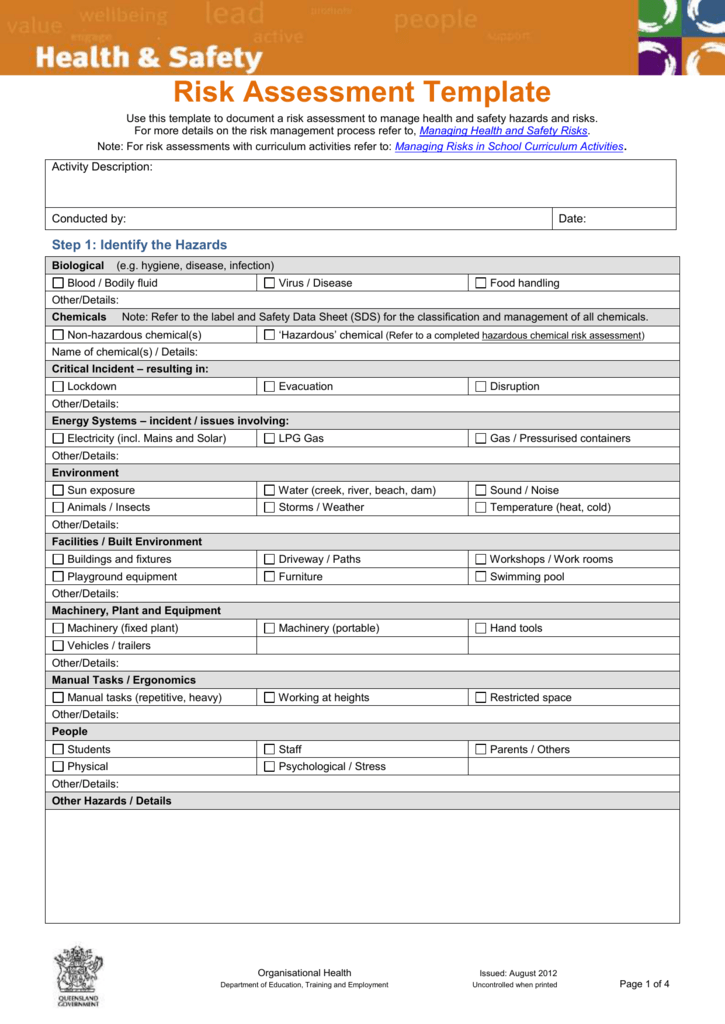
It is essential to maintaining regulatory compliance
Organizations must keep track of metrics and report on their processes in order to comply with regulatory requirements. These metrics are used to measure process adherence, and to identify risk/performance indicators. Metrics can also be used to determine whether regulatory changes have been made and what impact they will have on an enterprise. In order to predict future regulatory changes and demonstrate compliance, proactive organizations must monitor the change. This article will discuss some of the key metrics that must be monitored and reported.
FAQ
What is the difference in leadership and management?
Leadership is about influence. Management is about controlling others.
A leader inspires his followers while a manager directs the workers.
Leaders inspire people to achieve success. Managers keep their workers focused.
A leader develops people; a manager manages people.
What kind of people use Six Sigma
Six Sigma is well-known to those who have worked in operations research and statistics. But anyone can benefit from it.
Because it requires a high level of commitment, only those with strong leadership skills will make an effort necessary to implement it successfully.
What is the difference between TQM and Six Sigma?
The main difference in these two quality management tools lies in the fact that six sigma is focused on eliminating defects and total quality management (TQM), emphasizes improving processes and reducing costs.
Six Sigma is a methodology for continuous improvement. It emphasizes the elimination or minimization of defects through statistical methods such control charts and p charts.
This method has the goal to reduce variation of product output. This is done by identifying root causes and rectifying them.
Total Quality Management involves monitoring and measuring every aspect of the organization. This includes training employees to improve their performance.
It is frequently used as an approach to increasing productivity.
What does Six Sigma mean?
Six Sigma uses statistical analyses to locate problems, measure them, analyze root cause, fix problems and learn from the experience.
First, identify the problem.
Next, data is collected and analyzed to identify trends and patterns.
Then corrective actions are taken to solve the problem.
Finally, data will be reanalyzed to determine if there is an issue.
This cycle continues until there is a solution.
What is TQM exactly?
When manufacturing companies realized that price was not enough to compete, the industrial revolution brought about the quality movement. To remain competitive, they had to improve quality as well as efficiency.
In response to this need for improvement, management developed Total Quality Management (TQM), which focused on improving all aspects of an organization's performance. It involved continuous improvement, employee participation, and customer satisfaction.
What are some common mistakes managers make when managing people?
Managers can make their jobs more difficult than necessary.
They may not delegate enough responsibilities to staff and fail to give them adequate support.
A majority of managers lack the communication skills needed to motivate their team and lead them.
Managers set unrealistic expectations and make it difficult for their team.
Managers may choose to solve every problem all by themselves, instead of delegating to others.
How does a manager motivate his/her employees?
Motivation can be defined as the desire to achieve success.
Engaging in something fun can be a great way to get motivated.
Another way to get motivated is to see yourself as a contributor to the success of the company.
For example, if you want to become a doctor, you'll probably find it more motivating to see patients than to study medicine books all day.
The inner motivation is another type.
For example, you might have a strong sense of responsibility to help others.
You may even find it enjoyable to work hard.
If you don't feel motivated, ask yourself why.
You can then think of ways to improve your motivation.
Statistics
- As of 2020, personal bankers or tellers make an average of $32,620 per year, according to the BLS. (wgu.edu)
- Hire the top business lawyers and save up to 60% on legal fees (upcounsel.com)
- Our program is 100% engineered for your success. (online.uc.edu)
- 100% of the courses are offered online, and no campus visits are required — a big time-saver for you. (online.uc.edu)
- UpCounsel accepts only the top 5 percent of lawyers on its site. (upcounsel.com)
External Links
How To
How can you use the Kaizen method?
Kaizen means continuous improvement. Kaizen is a Japanese concept that encourages constant improvement by small incremental changes. It's a process where people work together to improve their processes continuously.
Kaizen is one of Lean Manufacturing's most efficient methods. The concept involves employees responsible for manufacturing identifying problems and trying to fix them before they become serious issues. This improves the quality of products, while reducing the cost.
Kaizen is about making everyone aware of the world around them. To prevent problems from happening, any problem should be addressed immediately. It is important that employees report any problems they see while on the job to their managers.
Kaizen is based on a few principles. The end product is always our starting point and we work toward the beginning. If we want to improve our factory for example, we start by fixing the machines that make the final product. Next, we fix the machines which produce components. Finally, we repair the workers who are directly involved with these machines.
This approach is called 'kaizen' because it focuses on improving everything steps by step. When we are done fixing the whole factory, we go back to the beginning and continue until we reach perfection.
Before you can implement kaizen into your business, it is necessary to learn how to measure its effectiveness. There are many methods to assess if kaizen works well. Another method is to see how many defects are found on the products. Another way is to check how much productivity has grown since kaizen was implemented.
You can also find out if kaizen works by asking yourself why you decided to implement it. It was because of the law, or simply because you wanted to save some money. Did you really believe that it would be a success factor?
Suppose you answered yes to any of these questions, congratulations! Now you're ready for kaizen.