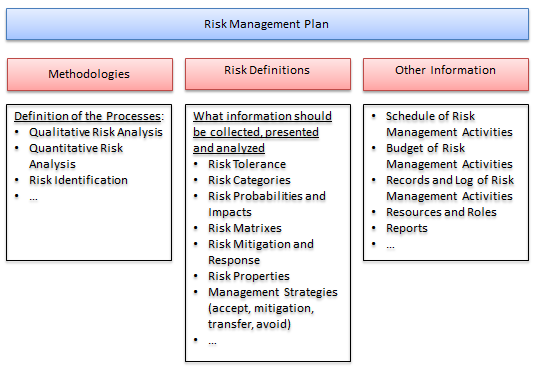
Five key elements are essential to supply chain success. These elements include collaboration, cost reduction, managing upstream and downstream business issues, and working with suppliers. It is crucial to identify and implement each of these elements in order for supply chain success. Additionally, supply chain success is affected by government and regulatory agencies.
Five strategy elements for supply chain success
Supply chain management is critical to the success of any organization, especially if you want to deliver on customer expectations. Your supply chain strategy should be based on customer needs in order to achieve this. This means that your fulfillment experience must be consistent with what the brand promises. So, for example, if a company promises speedy delivery, they must be able and willing to deliver. Customers also notice the small details. Customers value thoughtfulness which shows the thought process behind the brand.
Supply chain strategies that are successful must address issues related to suppliers. If a supplier is required to pay tariffs, it can lead to delays. It is best to source alternatives suppliers or to make bulk purchases before tariffs take effect. A supply chain software solution is also available to help businesses overcome delays. Software such as supply chain software can provide detailed information about inventory levels, inventory movement, and future needs.
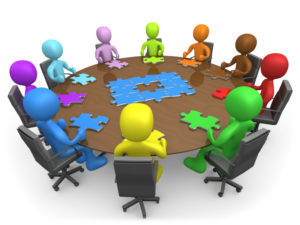
Governmental and regulatory bodies influence supply chain success
Many factors impact supply chain success. These include government policies and regulations. The United States spends federal dollars to promote domestic capacity and develop markets abroad. It also encourages collaboration between domestic and foreign companies. These mechanisms can be either public, private or cross-government. These efforts are made to assist companies in achieving their dual objectives. Companies rely on a trusted, robust global supply network.
This is particularly true for healthcare workers, since staff and patients' needs can have an impact on supply. For instance, hospitals may need to maintain stock of the right sizes and types of gloves for patients who require customized medical products. Financial managers might want to reduce healthcare costs and out-of-date products, while others may prefer specific brands or types. The lack of coordination and alignment of incentives can disrupt the flow of supply chains.
Working in collaboration with suppliers
Supply chain collaboration refers to the collaborative effort with suppliers to improve a company's ability to procure goods and services. There are many benefits for both sides. Collaboration is more flexible than the traditional customer/supplier relationship and focuses more heavily on creating value. Collaboration allows companies to see their suppliers as strategic partners that they can work with to increase competitive advantage.
Supply chain success depends on supplier collaboration. In order to maximize the value of collaboration, both parties must look for ways to improve their relationship with one another. One way to achieve this is to hold regular meetings with each of your suppliers. This will allow you to discuss their concerns and provide constructive feedback.
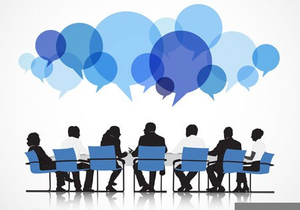
Managing upstream and downstream business issues
Supply chain management is the integration of many processes and tasks with an emphasis on delivering value for customers and other stakeholders. This can involve a range of issues including reputational, legal and operational risks. These issues can have an impact on the success or failure of a supply-chain. It is crucial to manage them.
Management professionals in supply chain must anticipate the key issues that will impact their business and devise strong management plans. They should also collaborate with their customers and suppliers to ensure that potential issues are addressed before they happen. Supply chain managers must also be vigilant and proactive in responding to global economic instability and increasing complexity. In some cases, tariffs may be imposed on trade routes by political circumstances. This could lead to increased costs and longer processing times for customs, as well slowing down international shipping.
FAQ
What's the difference between a program and a project?
A project is temporary; a program is permanent.
Projects usually have a goal and a deadline.
It is often performed by a team of people, who report back on someone else.
A program typically has a set goal and objective.
It is often implemented by one person.
What are the five management steps?
Planning, execution, monitoring and review are the five stages of any business.
Planning means setting goals for the long-term. Planning includes setting goals for the future.
Execution takes place when you actually implement the plans. You need to make sure they're followed by everyone involved.
Monitoring is the process of evaluating your progress toward achieving your objectives. Regular reviews should be done of your performance against targets or budgets.
Each year, reviews are held at the end. These reviews allow you to evaluate whether the year was successful. If not then, you can make changes to improve your performance next year.
After each year's review, evaluation occurs. It helps identify which aspects worked well and which didn't. It also provides feedback regarding how people performed.
What are management concepts, you ask?
Management Concepts are the principles and practices managers use to manage people and resources. These include topics such as human resource policies and job descriptions, performance assessments, training programs and employee motivation.
What is Six Sigma?
Six Sigma employs statistical analysis to identify problems, measure them and analyze root causes. Six Sigma also uses experience to correct problems.
First, identify the problem.
The next step is to collect data and analyze it in order to identify trends or patterns.
Then, corrective actions can be taken to resolve the problem.
Finally, data will be reanalyzed to determine if there is an issue.
This continues until the problem has been solved.
What are the steps involved in making a decision in management?
The decision-making process for managers is complex and multifaceted. This involves many factors including analysis, strategy and planning, implementation, measurement and evaluation, feedback, feedback, and others.
It is important to remember that people are human beings, just like you. They make mistakes. As such, there are always opportunities for improvement, especially when you put in the effort to improve yourself.
This video explains the process of decision-making in Management. We discuss the different types of decisions and why they are important, every manager should know how to navigate them. Here are some topics you'll be learning about:
Statistics
- The BLS says that financial services jobs like banking are expected to grow 4% by 2030, about as fast as the national average. (wgu.edu)
- 100% of the courses are offered online, and no campus visits are required — a big time-saver for you. (online.uc.edu)
- Hire the top business lawyers and save up to 60% on legal fees (upcounsel.com)
- This field is expected to grow about 7% by 2028, a bit faster than the national average for job growth. (wgu.edu)
- As of 2020, personal bankers or tellers make an average of $32,620 per year, according to the BLS. (wgu.edu)
External Links
How To
How do you do the Kaizen method?
Kaizen means continuous improvement. The term was coined in the 1950s at Toyota Motor Corporation and refers to the Japanese philosophy emphasizing constant improvement through small incremental changes. This is a collaborative process in which people work together to improve their processes continually.
Kaizen, a Lean Manufacturing method, is one of its most powerful. In this concept, employees who are responsible for the production line must identify problems that exist during the manufacturing process and try to solve them before they become big issues. This way, the quality of products increases, and the cost decreases.
The main idea behind kaizen is to make every worker aware of what happens around him/her. Correct any errors immediately to avoid future problems. So, if someone notices a problem while working, he/she should report it to his/her manager.
Kaizen is based on a few principles. Always start with the end product in mind and work our way back to the beginning. If we want to improve our factory for example, we start by fixing the machines that make the final product. Then, we fix the machines that produce components and then the ones that produce raw materials. Then, we fix those who work directly with the machines.
This approach is called 'kaizen' because it focuses on improving everything steps by step. Once we have finished fixing the factory, we return to the beginning and work until perfection.
You need to know how to measure the effectiveness of kaizen within your business. There are many ways to tell if kaizen is effective. Another way to determine if kaizen is working well is to look at the quality of the products. Another method is to determine how much productivity has improved since the implementation of kaizen.
A good way to determine whether kaizen has been implemented is to ask why. You were trying to save money or obey the law? Did you really believe it would lead to success?
Congratulations if you answered "yes" to any of the questions. You're ready to start kaizen.