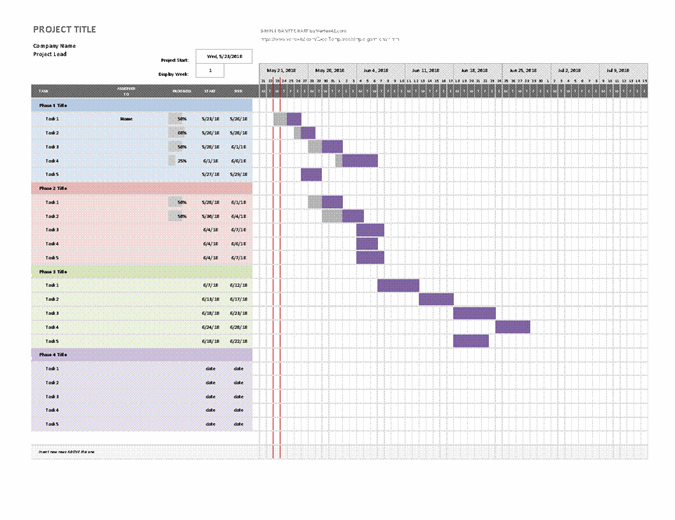
There are two main steps to follow when preparing a horse to lead change. The first is to change the horse's bent from left to right. This requires that the entire body bend. Next, the horse should push over onto the new lead with its right leg. This is known as a set-set-ask. These two steps serve to prepare the horse for a clean, smooth lead change.
Simple lead modifications
A simple lead change refers to the transition from a trot, canter, or walk to a trot. A flying change requires the horse to simultaneously switch his front and rear legs. Flying changes are necessary for advanced classes such as Western riding, jumping, and reining.
It is possible to make a simple change over a circle, along the centreline, and on a three-loop serpentine. It should be performed smoothly with good rhythm. Soft contact should also be used. It is crucial that the horse is comfortable and able to move away from the rider's leg with half-halts.
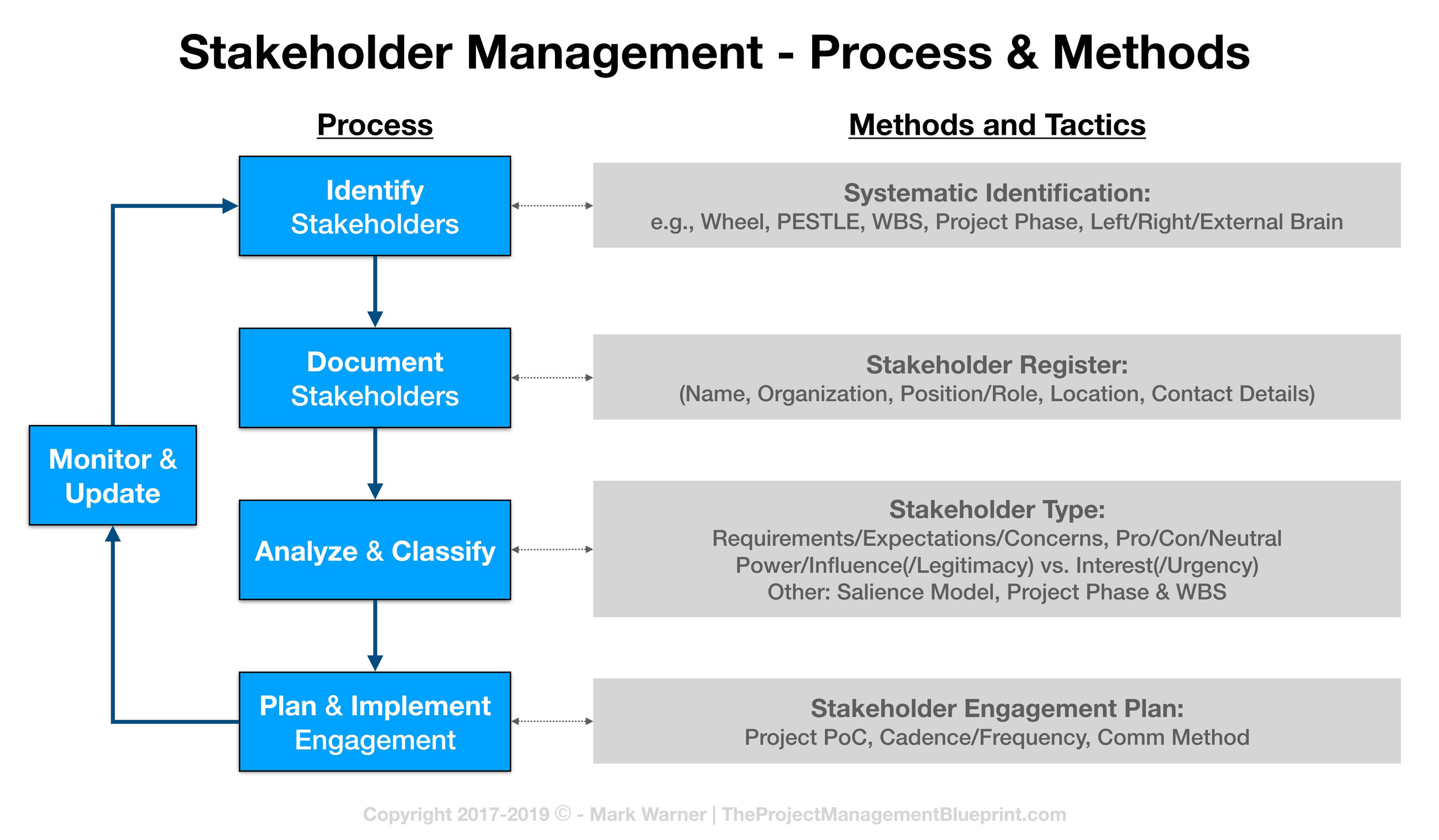
Impulsion
Horses must have strong impulsion in order to change their lead. You will have difficulty getting your horse to follow the lead. Counter canter exercises will help you develop impulsion. Even though a lead change can seem complicated, horses that can perform smoothly and effortlessly can become winners.
Recent research has shown that lead can have adverse effects on children and teens, as well as teenage pregnancy and drug abuse in animals. This could be due to lead's negative effects on executive functioning which can lead to poor impulse management.
Power is achieved by speaking truth to power
Sometimes it can be hard to speak truth. It involves going to the people who hold power in an organization and challenging their beliefs. When doing this, it is important to understand how those people came to their beliefs and to take their perspectives into account. Understanding what others think will help you find your truth. It is crucial to recognize the kind of power that you are challenging, as well as what the consequences.
A good leader will listen to you when you speak your truth. But he or she should avoid judging you as you do so. A leader who cares about you will seek you out and guide you in challenging power in a safe way.
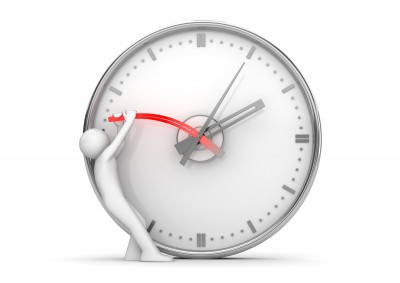
Campaign for TROY's Lead Change
The TROY University's Lead Change Campaign is dedicated to developing the next generation leaders. The university hopes to encourage students to put their talents and skills to work in their communities. This campaign is just one of the many examples of how TROY is committed to developing leaders.
Pinpointe’s email reporting capabilities provided TROY insight into the customer's responses to each email. This allowed Troy Group to optimize their email campaigns and increase open rates. They were also able to collect and send lead information to their sales reps through the email marketing system. The company's Pinpointe account is a crucial part of their email marketing strategy, as it has allowed them to boost sales visibility and reinforce the benefits of their products.
FAQ
What is the difference between leadership and management?
Leadership is about being a leader. Management is about controlling others.
Leaders inspire others, managers direct them.
Leaders motivate people to succeed; managers keep workers on track.
A leader develops people; a manager manages people.
What is the best way to motivate your employees as a manager?
Motivation is the desire to do well.
Enjoyable activities can motivate you.
You can also feel motivated by making a positive contribution to the success in the organization.
For example, if your goal is to become a physician, you will probably find it more motivational to see patients rather than to read a lot of medicine books.
The inner motivation is another type.
One example is a strong sense that you are responsible for helping others.
You might even enjoy the work.
If you don't feel motivated, ask yourself why.
Then, consider ways you could improve your motivation.
What are management theories?
Management concepts are the fundamental principles and practices that managers use when managing people and their resources. They cover topics such as job descriptions and performance evaluations, human resource policies, training programs, employee motivation, compens systems, organizational structure, among others.
Statistics
- Your choice in Step 5 may very likely be the same or similar to the alternative you placed at the top of your list at the end of Step 4. (umassd.edu)
- Hire the top business lawyers and save up to 60% on legal fees (upcounsel.com)
- Our program is 100% engineered for your success. (online.uc.edu)
- UpCounsel accepts only the top 5 percent of lawyers on its site. (upcounsel.com)
- 100% of the courses are offered online, and no campus visits are required — a big time-saver for you. (online.uc.edu)
External Links
How To
What is Lean Manufacturing?
Lean Manufacturing uses structured methods to reduce waste, increase efficiency and reduce waste. They were created by Toyota Motor Corporation in Japan in the 1980s. The main goal was to produce products at lower costs while maintaining quality. Lean manufacturing seeks to eliminate unnecessary steps and activities in the production process. It is made up of five elements: continuous improvement, continuous improvement, just in-time, continuous change, and 5S. Pull systems involve producing only what the customer wants without any extra work. Continuous improvement is constantly improving upon existing processes. Just-in-time refers to when components and materials are delivered directly to the point where they are needed. Kaizen stands for continuous improvement. Kaizen can be described as a process of making small improvements continuously. Fifth, the 5S stand for sort, set up in order to shine, standardize, maintain, and standardize. These five elements are combined to give you the best possible results.
Lean Production System
The lean production system is based on six key concepts:
-
Flow - focuses on moving information and materials as close to customers as possible.
-
Value stream mapping - break down each stage of a process into discrete tasks and create a flowchart of the entire process;
-
Five S's: Sort, Shine Standardize, Sustain, Set In Order, Shine and Shine
-
Kanban: Use visual signals such stickers, colored tape, or any other visual cues, to keep track your inventory.
-
Theory of constraints: identify bottlenecks in your process and eliminate them using lean tools, such as kanban board.
-
Just-in-time delivery - Deliver components and materials right to your point of use.
-
Continuous improvement - incremental improvements are made to the process, not a complete overhaul.