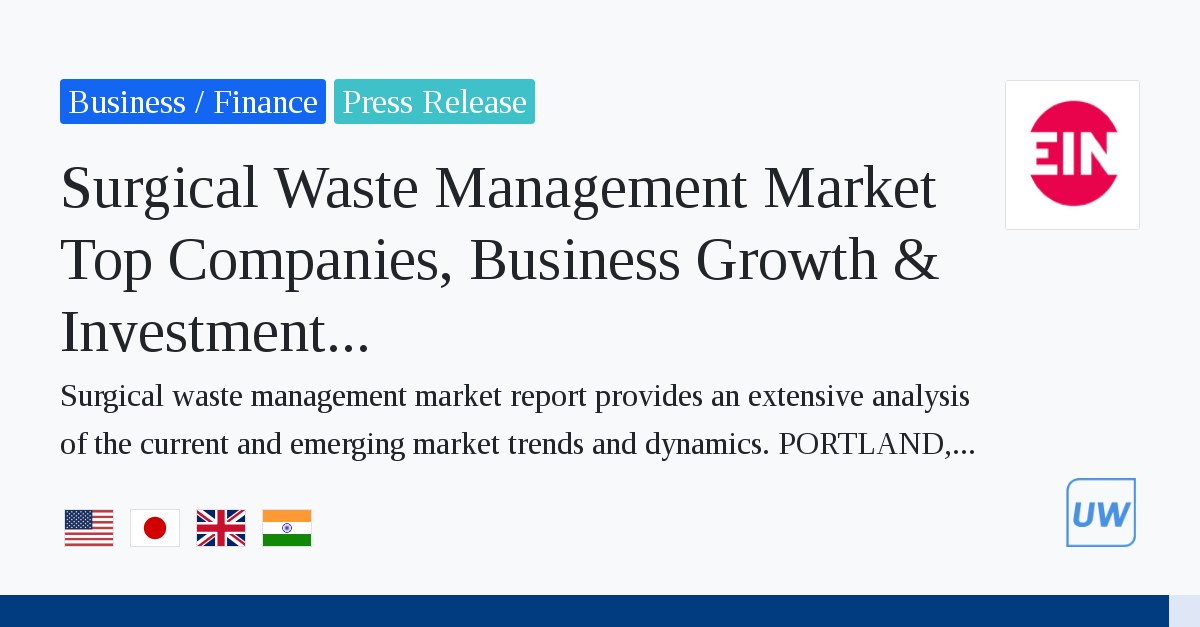
There are five key elements to supply chain success. These elements include collaboration with suppliers, reducing cost, and managing both upstream and downstream business problems. Identifying and implementing each of these elements is vital for supply chain success. You can also influence the success of supply chains by interacting with government agencies and regulators.
Five strategies to make supply chain success a reality
A company's success depends on its supply chain management, particularly if it wants to fulfill customer expectations. In order to achieve this, your supply chain strategy must be built around customer needs. This basically means that the fulfillment experience must match the brand's promises. A brand that promises fast delivery must be able deliver on its promise. Customers also notice the small details. They value thoughtfulness, which is a sign of the brand's thought process.
Supplier issues must be addressed in order to have a supply chain strategy that is successful. If a supplier is required to pay tariffs, it can lead to delays. The best way to overcome these delays is to source alternative suppliers or make bulk purchases before the tariffs are in effect. Additionally, supply chain software solutions can be used to overcome these delays. These software solutions can give accurate information about inventory levels and movement as well as future inventory needs.
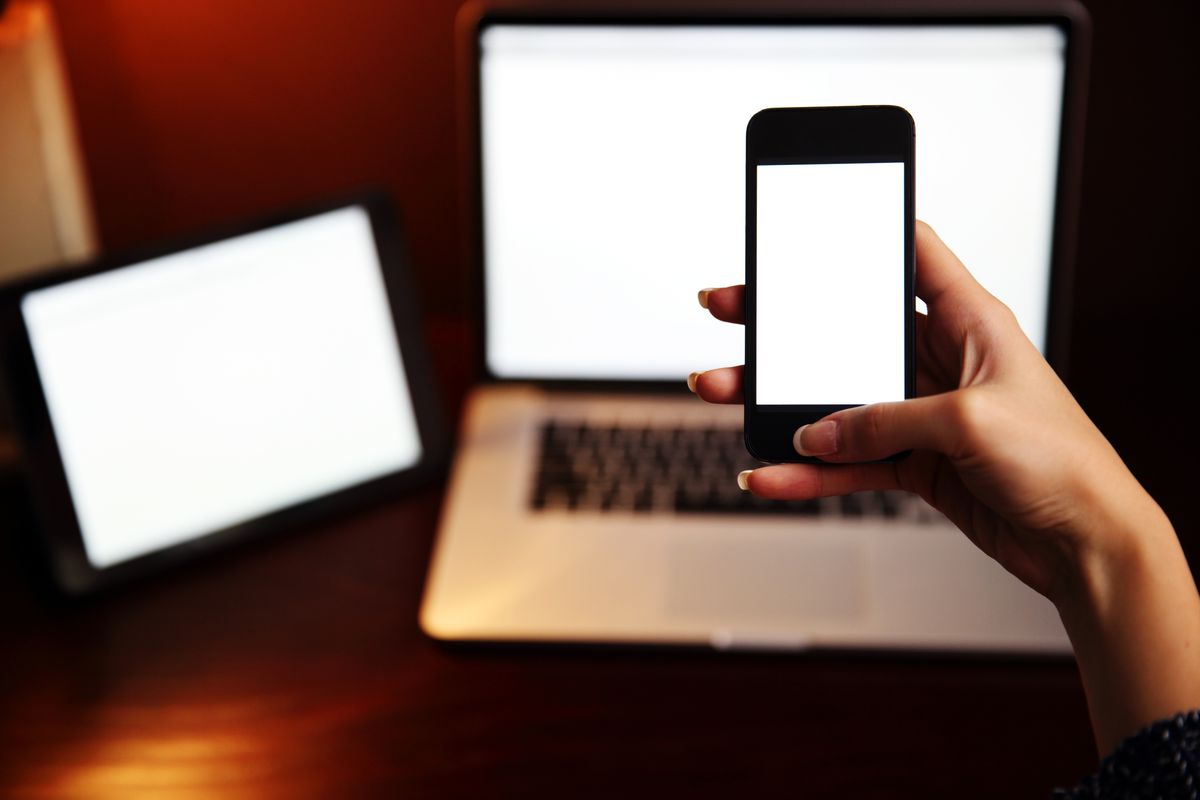
Success in supply chains is determined by the actions of government agencies and regulators
The success of supply chain operations is affected by several factors. The United States spends federal dollars to promote domestic capacity and develop markets abroad. It also encourages collaboration between domestic and foreign companies. These mechanisms may be private, public, or cross-government. These efforts aim to help companies achieve their dual objectives. This depends on a robust and trustworthy global supply chain.
This is especially true in healthcare, where staff and patients can impact the flow of supplies. Hospitals may have to stock the correct sizes of gloves while patients may require specific medical products. Financial managers might want to reduce healthcare costs and out-of-date products, while others may prefer specific brands or types. A lack of coordination can lead to disruptions in supply chains.
Collaboration with suppliers
Supply chain collaboration involves working with suppliers to increase the efficiency of a company’s procurement of goods or services. There are many benefits for both sides. Unlike the traditional customer-supplier relationship, collaboration is more flexible and focuses on creating value for both sides. Collaboration also allows companies to look at their suppliers as strategic partner with whom they can gain competitive advantage.
Supplier collaboration is critical to the success of a supply chain. Each party must find ways to improve the relationship between them in order to maximize collaboration's value. Regular meetings with your suppliers is one way to do this. You can discuss your concerns with them and give constructive feedback.
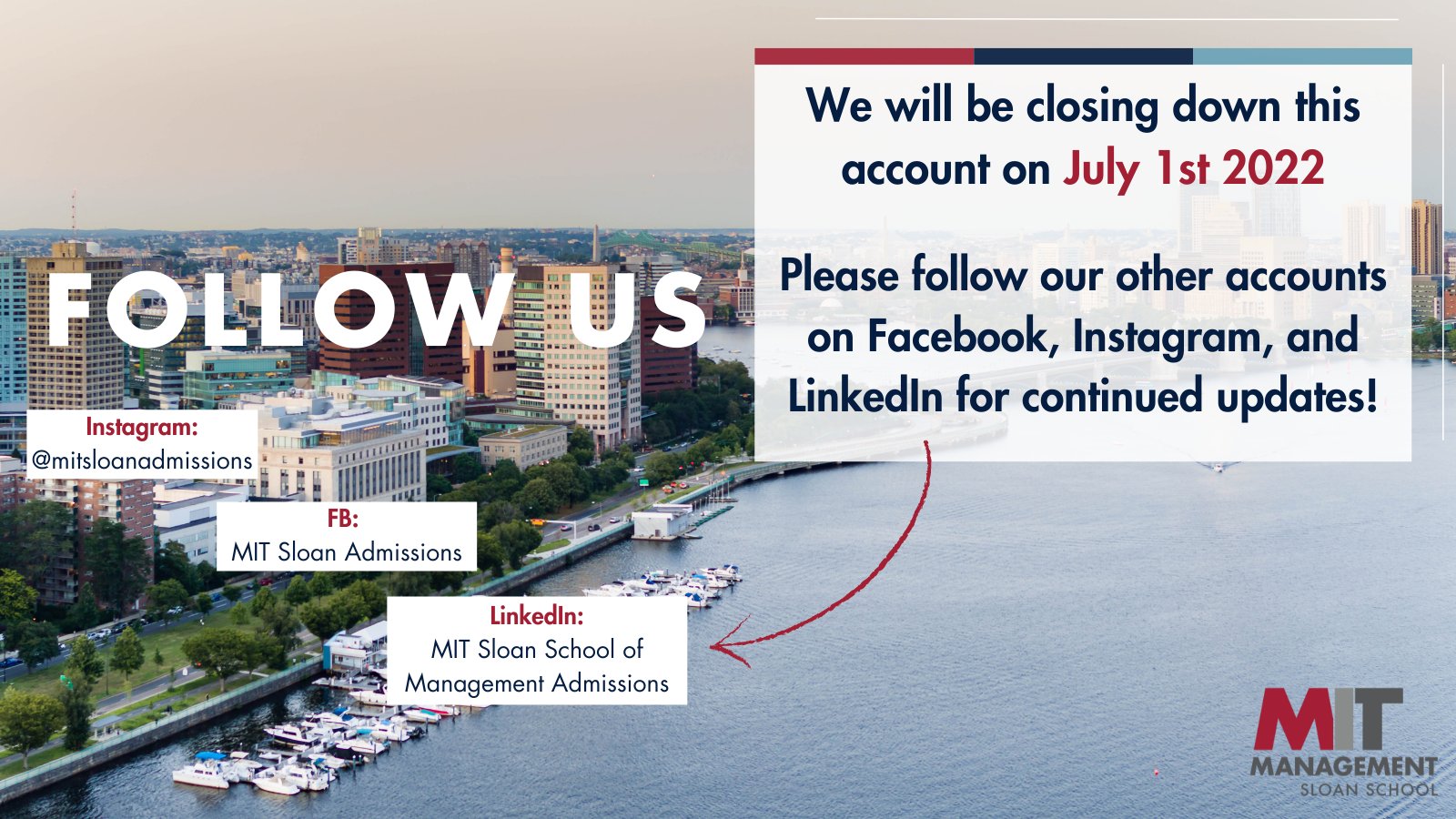
Problems relating to upstream or downstream businesses
Supply chain management consists of integrating a variety of processes and tasks, with a focus on delivering value to customers and other stakeholders. This involves many risks, including legal, financial and operational. This is why it is so important to manage them.
Professionals in supply chain management must be able anticipate and predict the most important issues impacting their businesses and create strong management plans. To address any potential problems, they need to create strong contracts and partner with suppliers and customers. The supply chain managers should be proactive and attentive in responding to economic instability around the world and rising complexity. Political situations, for example, may result in tariffs being placed on trade routes. This can increase costs and take longer customs processing times. It also slows down international shipping.
FAQ
What is the main difference between Six Sigma Six Sigma TQM and Six Sigma Six Sigma?
The main difference between these two quality management tools is that six sigma focuses on eliminating defects while total quality management (TQM) focuses on improving processes and reducing costs.
Six Sigma can be described as a strategy for continuous improvement. This approach emphasizes eliminating defects through statistical methods like control charts, Pareto analysis, and p-charts.
The goal of this method is to reduce variation in product output. This is achieved by identifying and addressing the root causes of problems.
Total Quality Management involves monitoring and measuring every aspect of the organization. It also involves training employees to improve performance.
It is commonly used as a strategy for increasing productivity.
How can a manager motivate his/her staff?
Motivation is the desire for success.
Engaging in something fun can be a great way to get motivated.
You can also be motivated by the idea of making a difference to the success and growth of your organization.
If you are a doctor and want to be one, it will likely be more rewarding to see patients than to read medical books every day.
The inner motivation is another type.
For example, you might have a strong sense of responsibility to help others.
Perhaps you enjoy working hard.
If you don't feel motivated, ask yourself why.
You can then think of ways to improve your motivation.
What are the 5 management processes?
These five stages are: planning, execution monitoring, review and evaluation.
Planning involves setting goals for the future. Planning includes setting goals for the future.
Execution is the actual execution of the plans. Everyone involved must follow them.
Monitoring is the act of monitoring your progress towards achieving your targets. Monitoring should include regular reviews of performance against goals and budgets.
Every year, there are reviews. They are a chance to see if everything went smoothly during the year. If not, it is possible to make improvements for next year.
After the annual review, evaluation takes place. It helps identify which aspects worked well and which didn't. It also provides feedback on the performance of people.
What is Six Sigma?
Six Sigma uses statistical analysis to find problems, measure them, analyze root causes, correct problems, and learn from experience.
The first step in solving a problem is to identify it.
Next, data will be collected and analyzed to determine trends and patterns.
The problem can then be fixed by taking corrective measures.
Finally, data will be reanalyzed to determine if there is an issue.
This continues until the problem has been solved.
Statistics
- The profession is expected to grow 7% by 2028, a bit faster than the national average. (wgu.edu)
- As of 2020, personal bankers or tellers make an average of $32,620 per year, according to the BLS. (wgu.edu)
- Your choice in Step 5 may very likely be the same or similar to the alternative you placed at the top of your list at the end of Step 4. (umassd.edu)
- Hire the top business lawyers and save up to 60% on legal fees (upcounsel.com)
- The BLS says that financial services jobs like banking are expected to grow 4% by 2030, about as fast as the national average. (wgu.edu)
External Links
How To
How do you use the 5S in your office?
Your workplace will be more efficient if you organize it properly. A clean desk, a neat room, and a well-organized space are all key factors in ensuring everyone is productive. The five "S"'s (Sort. Shine. Clean. Separate. And Store) help to maximize space and ensure efficiency. This session will go over each of these steps and show how they can be used in any setting.
-
Sort. You can get rid of all papers and clutter, so you don’t waste time looking for what you need. You should place things where you are most likely to use them. If you find yourself frequently referring to something, place it near the location where you do your research. You should also consider whether you really need to keep something around -- if it doesn't serve a useful function, get rid of it!
-
Shine. You should get rid of any items that could be harmful or cause injury to others. For example, if you have a lot of pens lying around, find a way to store them safely. A pen holder might be a good investment, as it will prevent you from losing pens.
-
Sweep. To prevent dirt buildup on furniture and other items, clean them regularly. To keep surfaces as clean as you can, invest in dusting equipment. To keep your workstation tidy, you can set aside an area for dusting and sweeping.
-
Separate. You will save time when disposing of trash by separating it into separate bins. To make it easier to throw away your trash without having to look for it, trash cans are often strategically placed throughout an office. It's a great idea to place trash bags beside each bin, so you don’t have to go through tons of garbage to find what it is.