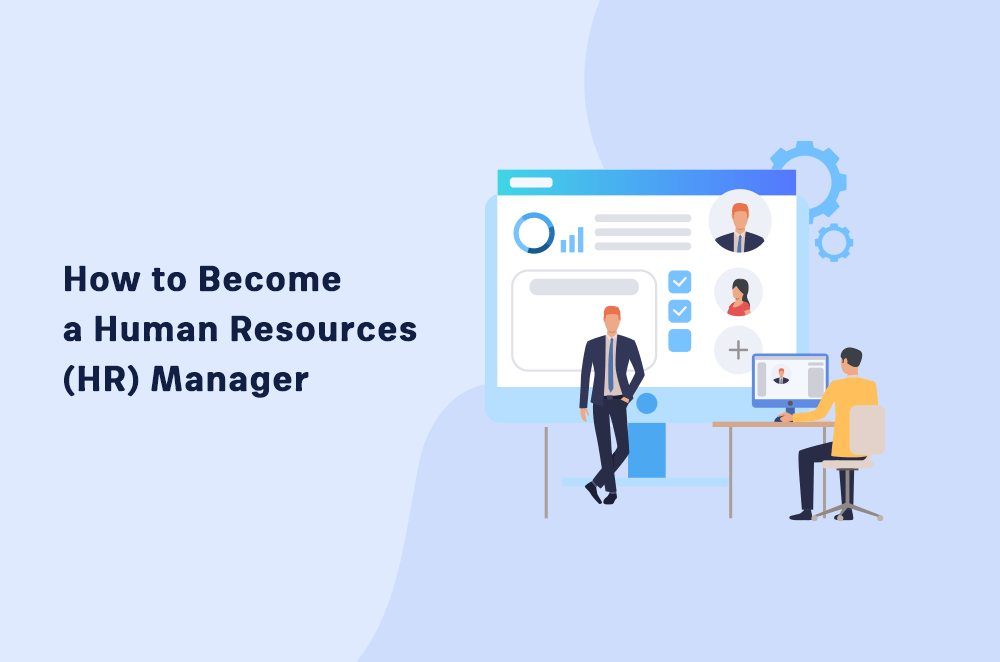
Micromanaging is an unacceptable and even harmful workplace practice. It is a sign of a toxic workplace. Micromanagement also violates basic human rights. To avoid being under such a toxic boss, it is important to know your rights as a worker. You have the right to confront a micromanager if he violates your basic rights. It can be a stressful and intimidating experience to confront a boss, but you must not let it get to you. There are many strategies you can use in dealing with bosses.
Micromanaging has its disadvantages
Micromanagement is a bad work style that can undermine trust between the bosses and their subordinates. Without trust, employees will lose their motivation to perform at their best and may not be as productive as they could otherwise. This can lead to high-performing employees being fired. This is a negative workplace environment that must be avoided if you want employees who work well.
Micromanaging creates distrust. Employees will view you as a despot, and this leads to a serious breakdown in the relationship between the two parties. This can impact productivity and the long-term longevity of employees' employment. Trust is a two-way street that is essential for building positive working relationships.
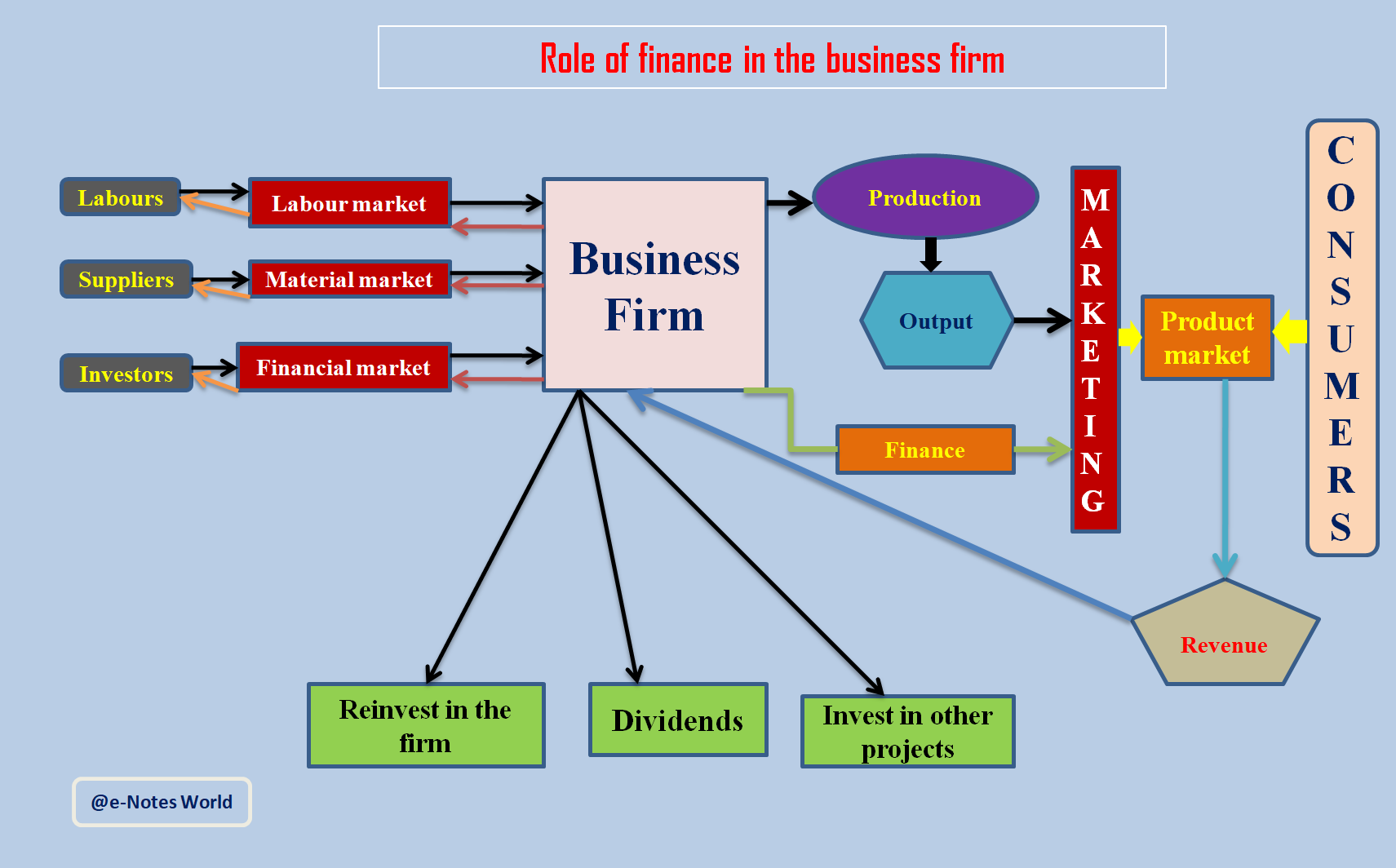
Signs of micromanaging
A micromanager will not only focus on the small things, but will also monitor employees' progress. This type of management can hinder productivity and lead to employee dissatisfaction. Micromanagers often require detailed progress reports from employees and criticize them for their work without taking into account the context.
Micromanaging can also cause a lack of trust in employees, as a micromanager often refuses to delegate. They might be more interested in frequent updates and meetings.
Micromanaging and its effects on employees
Micromanagement negatively affects the morale of employees. Employees feel like failures and give up trying, which can lead to micromanagement. Employees will eventually lose their motivation and initiative and their job satisfaction will drop. Micromanagement can also have a negative impact on an employee's personal and professional life. This can lead to strained relationships.
Micromanagement can also be detrimental to employee creativity. This discourages employees to come up with new ideas or step outside their job descriptions. It can also make employees feel unsafe, which can result in increased staff turnover.
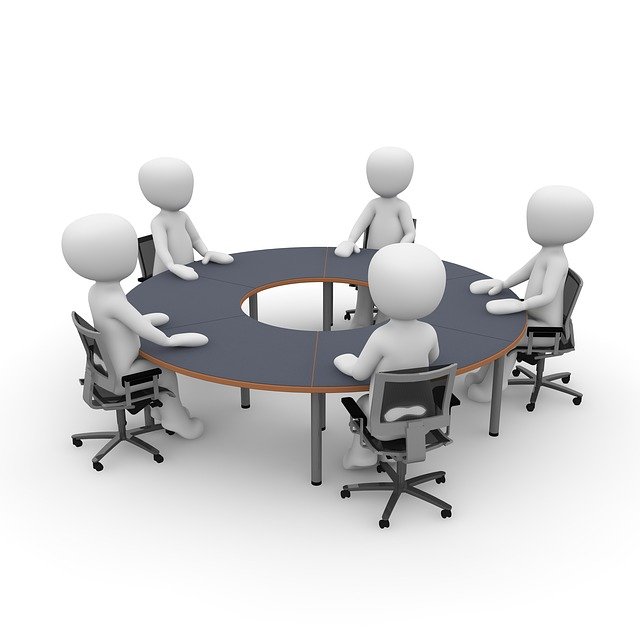
Here are some ways to handle a boss who micromanages
Although it can be stressful to deal with a micromanaging boss, there is a way to make this a less stressful situation. First, remember that micromanagers often do what they do because of their own anxieties. Do not be afraid to tell details even if they could slow down the project.
It is possible to also ask questions about the motivations of micromanagers. Many micromanagers are caring and concerned about the performance of their employees. You can ask them questions to find out if they are being unreliable or trusting.
FAQ
It seems so difficult sometimes to make sound business decisions.
Complex business systems have many moving parts. They require people to manage multiple priorities and deal with uncertainty and complexity.
Understanding how these factors impact the whole system is key to making informed decisions.
To do this, you must think carefully about what each part of the system does and why. Then, you need to think about how these pieces interact with one another.
Also, you should ask yourself if there have been any assumptions in your past behavior. If so, it might be worth reexamining them.
Asking for assistance from someone else is a good idea if you are still having trouble. They may see things differently from you and have insights that could help you find a solution.
What are the steps involved in making a decision in management?
Managers have to make complex decisions. This involves many factors including analysis, strategy and planning, implementation, measurement and evaluation, feedback, feedback, and others.
When managing people, the most important thing to remember is that they are just human beings like you and make mistakes. You are always capable of improving yourself, and there's always room for improvement.
This video explains the process of decision-making in Management. We will explain the importance of different types decisions and how every manager can make them. Here are some topics you'll be learning about:
What is Six Sigma?
This is a method of quality improvement that emphasizes customer service, continuous learning, and customer service. The goal is to eradicate defects through statistical techniques.
Motorola developed Six Sigma in 1986 to help improve its manufacturing processes.
The idea spread quickly throughout the industry, and today, many organizations are using six sigma methods to improve product design, production, delivery, and customer service.
What is the role of a manager in a company?
Managers' roles vary from industry to industry.
A manager is generally responsible for overseeing the day to day operations of a company.
He/she ensures the company meets its financial commitments and produces goods/services that customers demand.
He/she will ensure that employees follow all rules and regulations, and adhere to quality standards.
He/she oversees marketing campaigns and plans new products.
What is the difference in Six Sigma and TQM?
The main difference between these two quality-management tools is that six-sigma concentrates on eliminating defects while total QM (TQM), focuses upon improving processes and reducing expenses.
Six Sigma can be described as a strategy for continuous improvement. This approach emphasizes eliminating defects through statistical methods like control charts, Pareto analysis, and p-charts.
This method has the goal to reduce variation of product output. This is done by identifying root causes and rectifying them.
Total Quality Management involves monitoring and measuring every aspect of the organization. Training employees is also part of total quality management.
It is often used as a strategy to increase productivity.
What are the 3 basic management styles?
These are the three most common management styles: participative (authoritarian), laissez-faire (leavez-faire), and authoritarian. Each style has its own strengths and weaknesses. Which style do yo prefer? Why?
Authority - The leader is the one who sets the direction and expects everyone in the organization to follow it. This style is best when the organization has a large and stable workforce.
Laissez faire - Each individual can decide for himself/herself. This style is best when the organization has a small but dynamic group.
Participative: The leader listens to everyone's ideas and suggestions. This style is best for small organizations where everyone feels valued.
How do you effectively manage employees?
Achieving employee happiness and productivity is key to managing them effectively.
It also means having clear expectations of their behavior and keeping track of their performance.
Managers need to establish clear goals for their team and for themselves.
They must communicate clearly with their staff. They should also ensure that they both reward high performers and discipline those who are not performing to their standards.
They should also keep records of all activities within their team. These include:
-
What was the result?
-
How much work were you able to accomplish?
-
Who did it and why?
-
How did it get done?
-
Why did it happen?
This data can be used to evaluate and monitor performance.
Statistics
- Hire the top business lawyers and save up to 60% on legal fees (upcounsel.com)
- Our program is 100% engineered for your success. (online.uc.edu)
- The profession is expected to grow 7% by 2028, a bit faster than the national average. (wgu.edu)
- UpCounsel accepts only the top 5 percent of lawyers on its site. (upcounsel.com)
- 100% of the courses are offered online, and no campus visits are required — a big time-saver for you. (online.uc.edu)
External Links
How To
What is Lean Manufacturing?
Lean Manufacturing methods are used to reduce waste through structured processes. They were created by Toyota Motor Corporation in Japan in the 1980s. The main goal was to produce products at lower costs while maintaining quality. Lean manufacturing focuses on eliminating unnecessary steps and activities from the production process. It is composed of five fundamental elements: continuous improvement; pull systems, continuous improvements, just-in–time, kaizen, continuous change, and 5S. Pull systems allow customers to get exactly what they want without having to do extra work. Continuous improvement means continuously improving on existing processes. Just-intime refers the time components and materials arrive at the exact place where they are needed. Kaizen means continuous improvement. Kaizen involves making small changes and improving continuously. Fifth, the 5S stand for sort, set up in order to shine, standardize, maintain, and standardize. These five elements are combined to give you the best possible results.
The Lean Production System
Six key concepts form the foundation of the lean production system:
-
Flow - The focus is on moving information and material as close as possible to customers.
-
Value stream mapping - Break down each stage in a process into distinct tasks and create an overview of the whole process.
-
Five S's, Sort, Set in Order, Shine. Standardize. and Sustain.
-
Kanban – visual signals like colored tape, stickers or other visual cues are used to keep track inventory.
-
Theory of constraints: Identify bottlenecks and use lean tools such as kanban boards to eliminate them.
-
Just-in-time - deliver components and materials directly to the point of use;
-
Continuous improvement: Make incremental improvements to the process instead of overhauling it completely.