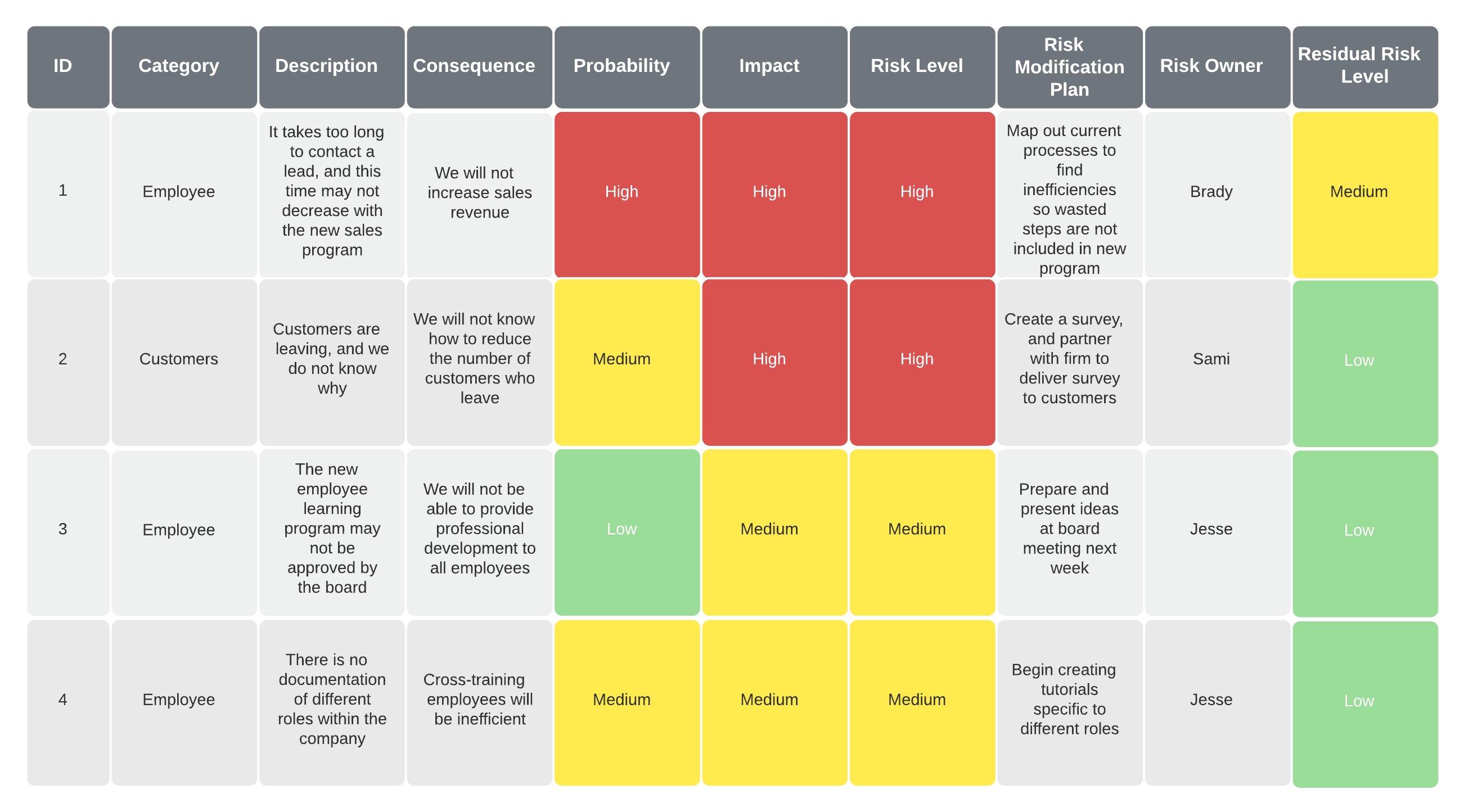
The creation of risk management plans is an important part of any project, from small to large. The risk management plan that you create will help to mitigate any risks associated with a project. Here are some tips for creating a risk management plan. Before you begin writing, you need to assess all of the risks. This will help to determine the most significant and likely risks, and formulate a plan that can be used to mitigate them. You should ensure that your plan is current and complete so you can implement it quickly.
Plan for risk management
A risk management strategy is a powerful tool for managing your risks and increasing your chances of success. It will help reduce or completely eliminate potential risks and make it easier for you to prepare your team. A well-defined risk management plan will ensure your project has the best chance of meeting its objectives. However, if it's not done properly, it may expose your project to problems. A risk management plan should be simple, concise, and easily understood.
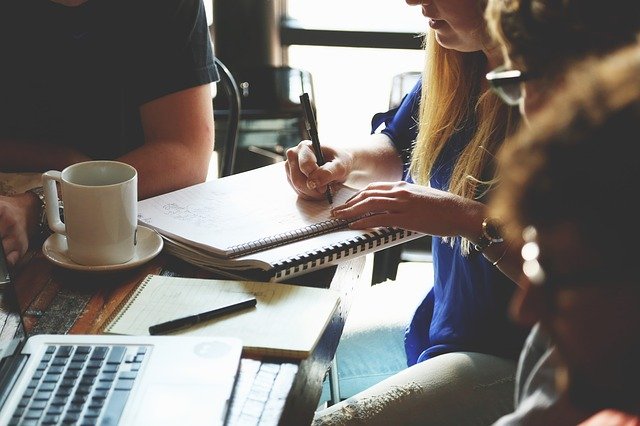
Steps to create a plan
The first step in creating a risk management strategy is to identify potential risks and solutions. This should be done in collaboration with team members and experts. The next step is to identify risks and determine the resources necessary to mitigate or prevent them. It is important to include a communication plan in your risk management plan. This will help you keep the team on track. It should also include a list listing all possible solutions and measures that can be taken to mitigate risks.
Analyze project risks
A project's overall plan should include a risk management program. Risk analysis can help identify which aspects of a given project are most at high risk. Once potential risks are identified, project managers can decide what steps to take to mitigate them. A sound risk management plan will include steps that can be taken to minimize risks and minimize the impact. This article will cover the many steps involved in risk management, as well as how to accurately analyze project risks.
Develop a plan to mitigate them
It is critical to have a risk management strategy in place. This plan will help your business identify and prioritize potential risks, and help minimize the negative impacts of those risks. But this is not a job for one person. You will need to educate employees about risk and train them on mitigation strategies. Your risk mitigation plan will only be as effective if you have the right people and the right resources. By using a risk management system, you can keep your business running smoothly.
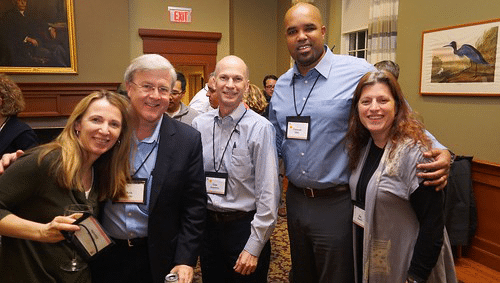
Archive your plan
In some organisations, archiving your risk management plan is mandatory. Some risk management plans may not work for all projects. Another option is to use a past project's risk management plan as a basis for future projects. Although it may not be necessary to archive your risk management plan, it is a good idea. Here are some tips to help you archive your plan. We hope these tips are helpful to you!
FAQ
What are management principles?
Management concepts are the principles and practices used by managers to manage people, resources. They cover topics such as job descriptions and performance evaluations, human resource policies, training programs, employee motivation, compens systems, organizational structure, among others.
What is the difference between management and leadership?
Leadership is all about influencing others. Management is about controlling others.
A leader inspires followers while a manager directs workers.
Leaders motivate people to succeed; managers keep workers on track.
A leader develops people; a manager manages people.
What are some of the common mistakes made by managers?
Sometimes managers make it harder for their employees than is necessary.
They might not give enough support and delegate the right responsibilities to their staff.
Managers often lack the communication skills necessary to motivate and guide their teams.
Some managers set unrealistic expectations for their staff.
Some managers may try to solve every problem themselves instead of delegating responsibility to others.
What is the difference in Six Sigma and TQM?
The major difference between the two tools for quality management is that six Sigma focuses on eliminating defect while total quality control (TQM), on improving processes and decreasing costs.
Six Sigma can be described as a strategy for continuous improvement. This method emphasizes eliminating defects using statistical methods such p-charts, control charts, and Pareto analysis.
The goal of this method is to reduce variation in product output. This is achieved by identifying and addressing the root causes of problems.
Total quality management involves measuring and monitoring all aspects of the organization. This includes training employees to improve their performance.
It is often used as a strategy to increase productivity.
What is TQM?
The industrial revolution saw the realization that prices alone were not sufficient to sustain manufacturing companies. This led to the birth of quality. To remain competitive, they had to improve quality as well as efficiency.
In response to this need for improvement, management developed Total Quality Management (TQM), which focused on improving all aspects of an organization's performance. It included continuous improvement, employee involvement and customer satisfaction.
What can a manager do to improve his/her management skillset?
You can improve your management skills by practicing them at all times.
Managers must constantly monitor the performance of their subordinates.
You should immediately take action if you see that your subordinate is not performing as well as you would like.
You should be able to identify what needs improvement and how to improve things.
What are the steps that management takes to reach a decision?
The decision-making process for managers is complex and multifaceted. It includes many factors such as analysis, strategy planning, implementation and measurement. Evaluation, feedback and feedback are just some of the other factors.
The key thing to remember when managing people is that they are human beings just as you are and therefore make mistakes. You can always improve your performance, provided you are willing to make the effort.
This video shows you how management makes decisions. We will explain the importance of different types decisions and how every manager can make them. The following topics will be covered.
Statistics
- The BLS says that financial services jobs like banking are expected to grow 4% by 2030, about as fast as the national average. (wgu.edu)
- The average salary for financial advisors in 2021 is around $60,000 per year, with the top 10% of the profession making more than $111,000 per year. (wgu.edu)
- Our program is 100% engineered for your success. (online.uc.edu)
- This field is expected to grow about 7% by 2028, a bit faster than the national average for job growth. (wgu.edu)
- The profession is expected to grow 7% by 2028, a bit faster than the national average. (wgu.edu)
External Links
How To
What is Lean Manufacturing?
Lean Manufacturing techniques are used to reduce waste while increasing efficiency by using structured methods. They were created by Toyota Motor Corporation in Japan in the 1980s. The primary goal was to make products with lower costs and maintain high quality. Lean manufacturing eliminates unnecessary steps and activities from a production process. It includes five main elements: pull systems (continuous improvement), continuous improvement (just-in-time), kaizen (5S), and continuous change (continuous changes). Pull systems involve producing only what the customer wants without any extra work. Continuous improvement refers to continuously improving existing processes. Just-intime refers the time components and materials arrive at the exact place where they are needed. Kaizen is continuous improvement. This can be achieved by making small, incremental changes every day. Finally, 5S stands for sort, set in order, shine, standardize, and sustain. These five elements can be combined to achieve the best possible results.
The Lean Production System
Six key concepts form the foundation of the lean production system:
-
Flow: The goal is to move material and information as close as possible from customers.
-
Value stream mapping: This is a way to break down each stage into separate tasks and create a flowchart for the entire process.
-
Five S's - Sort, Set In Order, Shine, Standardize, and Sustain;
-
Kanban is a visual system that uses visual cues like stickers, colored tape or stickers to keep track and monitor inventory.
-
Theory of constraints: Identify bottlenecks and use lean tools such as kanban boards to eliminate them.
-
Just-in time - Get components and materials delivered right at the point of usage;
-
Continuous improvement - make incremental improvements to the process rather than overhauling it all at once.