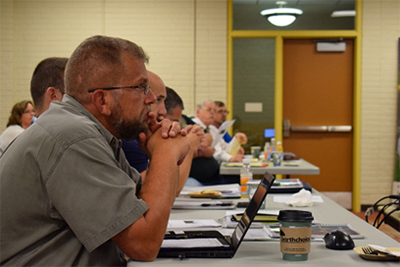
If you're ready to take the next step in your career, consider earning your bachelor's in supply chain management. The 120-credit program will give you a solid understanding of logistics and operations management. The program is accredited by NEASC, and includes topics such as continuous improvement tools. U.S. News has ranked this program as a top-rated online program.
Degree programs in supply chain management online
You can advance your career by completing an online supply chain management degree program. These programs provide training in logistics, warehouse operations and communication and help you meet today's challenges. You'll learn how you can make deals with suppliers and optimize warehouse efficiency. These programs can be completed part-time, or full-time.
The cost of an online degree in supply chain management can vary depending on which program you choose. It could be as low as $8550. Consider your location as well, since many colleges will charge higher tuition for students living outside of their home state. Private scholarships are also available to finance your education. To add to the tuition cost, you will also need to account for technology costs. The cost of a degree in supply chain management for a full time student is typically between $36,000- $64,000
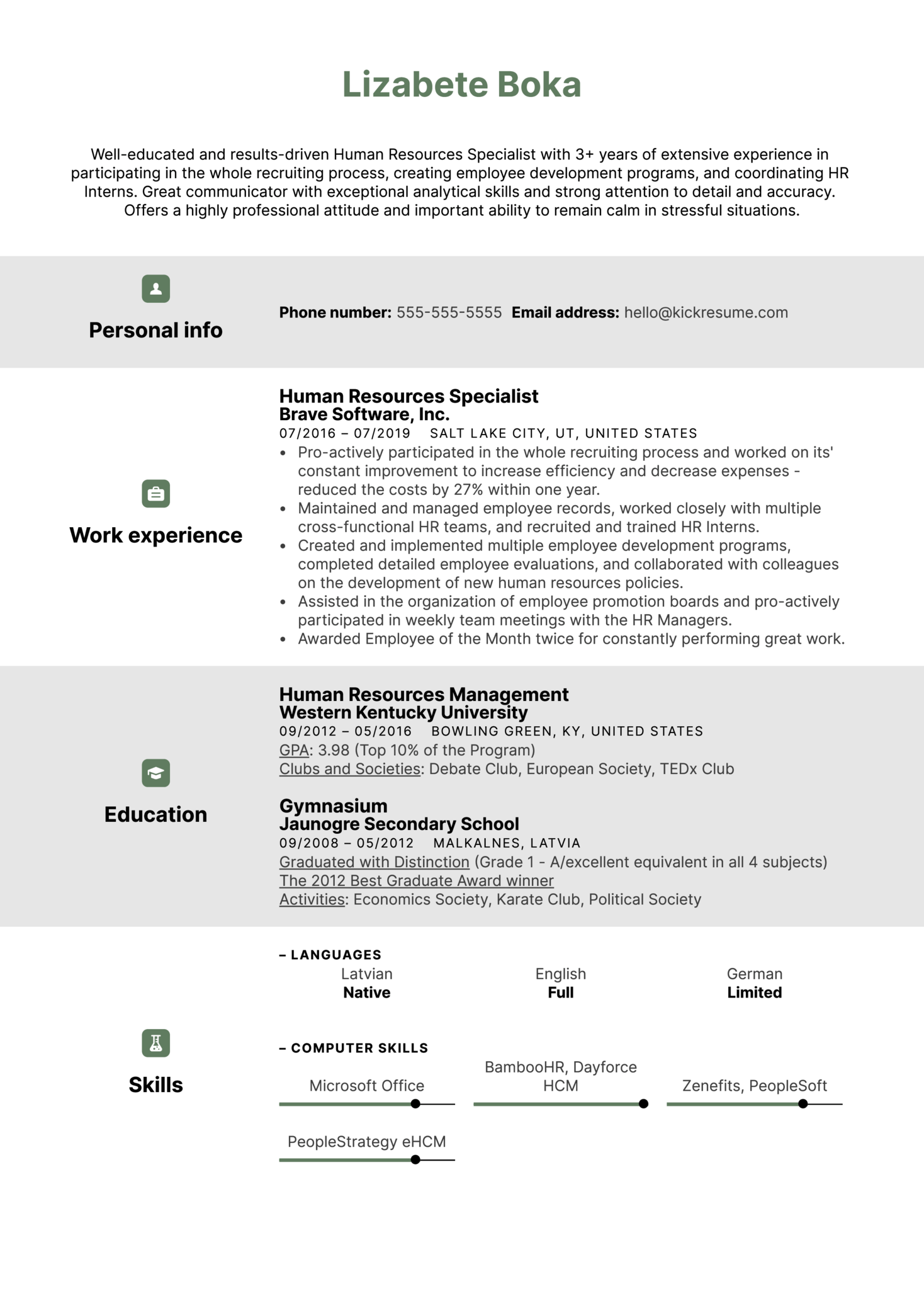
Accredited supply chain management degree programs
A degree program in supply chain management can be accredited to help students gain the skills necessary for success. These online degrees are available in many areas. Some degree programs include a capstone project, an internship, or study abroad. While the curriculum for these programs may not be as comprehensive as a conventional degree, they are designed to be flexible.
Supply chain management is a career that requires a wide range of skills. In order to succeed in this field, candidates need to have a strong business background and an understanding of information systems.
Distance Learning Supply Chain Management Degree Programs
Many institutions offer online degrees in supply chain management. Some schools are accredited by Higher Learning Commission. Others are not. Online students can access the same resources and support that students who are on-campus. Online degree programs that offer the highest quality can combine traditional classroom teaching with online classes.
Costs for an online degree in supply-chain management vary depending on many factors. An important factor to consider is whether the student is a resident or non-resident of the state in which the school is located. Some colleges charge higher tuition for students living outside the state. Others charge a flat rate to all students. Students should also factor in technology costs. For tuition and fees, students should expect to budget between $36,000- $64,000 on average.
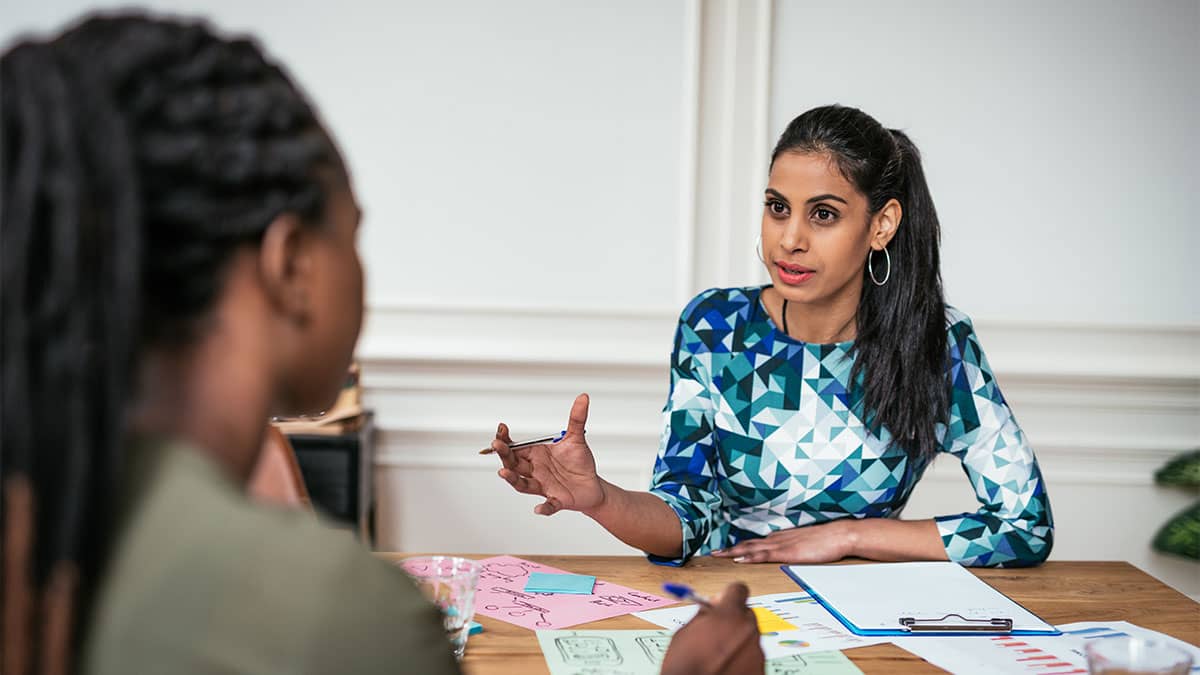
Here are the top supply chain management degree programs
According to the latest ranking of supply-chain management degree programs, Arkansas defends its pole position with a spot at the Top 3. The University of South Carolina (UCS) and the University of Tennessee (UTM) round out the top three. But the top schools are usually more expensive and more competitive. In recent years, the emphasis on supply chain management has shifted towards sustainability and risk mitigation.
USC Marshall School of Business is another reputable institution that has a flexible program that can be completed on campus or online. Other top-ranked institutions include Trinity Business School, Alliance Manchester Business School, and Politecnico di Milano School of Management. The top 10 include Purdue University, the University of Washington Foster School of Business and the University of Washington School of Management. The rankings are based in part on more than 50,000 business leaders who attended business schools around the globe.
FAQ
How does Six Sigma work
Six Sigma uses statistical analysis to find problems, measure them, analyze root causes, correct problems, and learn from experience.
The first step is identifying the problem.
Next, data will be collected and analyzed to determine trends and patterns.
The problem can then be fixed by taking corrective measures.
Finally, data will be reanalyzed to determine if there is an issue.
This continues until you solve the problem.
What is the difference in a project and program?
A project is temporary while a programme is permanent.
A project has usually a specified goal and a time limit.
It is often carried out by a team of people who report back to someone else.
A program usually has a set of goals and objectives.
It is often done by one person.
What are the steps in the decision-making process in management?
Managers have to make complex decisions. It includes many factors such as analysis, strategy planning, implementation and measurement. Evaluation, feedback and feedback are just some of the other factors.
It is important to remember that people are human beings, just like you. They make mistakes. You can always improve your performance, provided you are willing to make the effort.
In this video, we explain what the decision-making process looks like in Management. We discuss different types of decisions as well as why they are important and how managers can navigate them. The following topics will be covered:
Statistics
- Our program is 100% engineered for your success. (online.uc.edu)
- As of 2020, personal bankers or tellers make an average of $32,620 per year, according to the BLS. (wgu.edu)
- The average salary for financial advisors in 2021 is around $60,000 per year, with the top 10% of the profession making more than $111,000 per year. (wgu.edu)
- 100% of the courses are offered online, and no campus visits are required — a big time-saver for you. (online.uc.edu)
- The profession is expected to grow 7% by 2028, a bit faster than the national average. (wgu.edu)
External Links
How To
How do you do the Kaizen method?
Kaizen means continuous improvement. This Japanese term refers to the Japanese philosophy of continuous improvement that emphasizes incremental improvements and constant improvement. This is a collaborative process in which people work together to improve their processes continually.
Kaizen is one of the most effective methods used in Lean Manufacturing. The concept involves employees responsible for manufacturing identifying problems and trying to fix them before they become serious issues. This improves the quality of products, while reducing the cost.
Kaizen is the idea that every worker should be aware of what is going on around them. So that there is no problem, you should immediately correct it if something goes wrong. Report any problem you see at work to your manager.
When doing kaizen, there are some principles we must follow. Always start with the end product in mind and work our way back to the beginning. We can improve the factory by first fixing the machines that make it. Next, we fix the machines which produce components. Finally, we repair the workers who are directly involved with these machines.
This method is known as kaizen because it focuses upon improving every aspect of the process step by step. After we're done with the factory, it's time to go back and fix the problem.
It is important to understand how to measure the effectiveness and implementation of kaizen in your company. There are many methods to assess if kaizen works well. One way is to examine the amount of defects on the final products. Another way is to check how much productivity has grown since kaizen was implemented.
A good way to determine whether kaizen has been implemented is to ask why. It was because of the law, or simply because you wanted to save some money. Did you really think that it would help you achieve success?
Let's say you answered yes or all of these questions. Congratulations! You are ready to start kaizen.