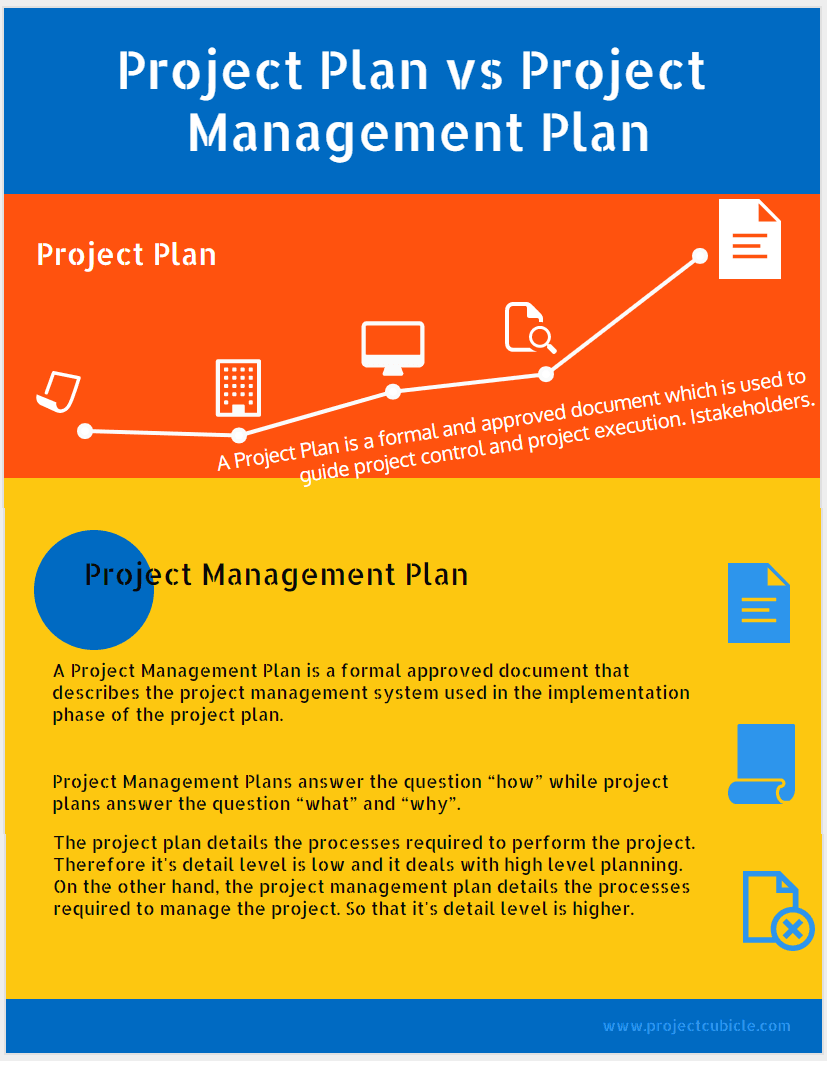
The five essential elements of supply chain success are: These elements include working together with suppliers, reducing costs, managing upstream business issues, as well as working collaboratively. Supply chain success depends on each element being identified and implemented. There are also regulatory and government bodies that can influence supply chain success.
Five strategies for success in supply chain
A company's success depends on its supply chain management, particularly if it wants to fulfill customer expectations. You must build your supply chain strategy around customer needs to be successful. This means that the fulfillment experience must live up to the brand's promises. A brand that promises fast delivery must be able deliver on its promise. Customers also pay attention to the little things. Customers also appreciate thoughtfulness. This is an indication of the thought process behind the brand.
Supply chain strategies that are successful must address issues related to suppliers. It can be a problem if suppliers have to pay tariffs. It is best to source alternatives suppliers or to make bulk purchases before tariffs take effect. These delays can be overcome by a supply chain solution. This software provides accurate information about inventory levels, movements, and future inventory requirements.
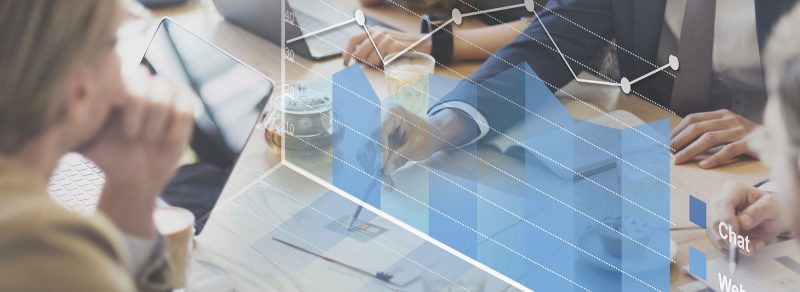
Governmental and regulatory bodies influence supply chain success
The success of supply chain operations is affected by several factors. The United States spends federal money to develop foreign markets and promote domestic capacity. At the same time, it encourages cooperation between domestic companies and countries. These mechanisms may be private, public, or cross-government. These efforts are meant to assist companies with their dual goals, which depend on a strong and trusted global supply chain.
This is especially relevant in the healthcare sector, where the needs of staff and patients can affect the supply flow. Some hospitals might need to have the right size gloves in stock, while others may require specialized medical products. Finance managers may also want to cut healthcare costs by reducing out-of date products. Others may prefer certain brands or types. The lack of coordination and alignment of incentives can disrupt the flow of supply chains.
Cooperation with suppliers
Supply chain collaboration involves working with suppliers to increase the efficiency of a company’s procurement of goods or services. It has a number of benefits for both companies. Collaboration is more flexible and creates value for both companies than the traditional customer/supplier partnership. Companies can also view their suppliers and collaborate with them to achieve competitive advantage.
Collaboration between suppliers is crucial to the success and sustainability of a supply chain. Collaboration is only possible if both parties look for ways they can improve their relationship. This can be achieved by having regular meetings with all your suppliers. This will give you the opportunity to listen to their concerns and offer constructive feedback.
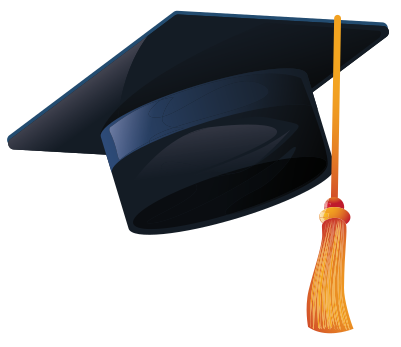
Managing upstream and downstream business issues
Supply chain management is the integration of many processes and tasks with an emphasis on delivering value for customers and other stakeholders. This involves many risks, including legal, financial and operational. Because they can directly impact the success of a supply network, it is vital to manage these issues.
Management professionals in supply chain must anticipate the key issues that will impact their business and devise strong management plans. In addition, they must build strong contracts and collaborate with their suppliers and customers to address potential issues before they arise. The supply chain managers should be proactive and attentive in responding to economic instability around the world and rising complexity. For example, political situations may introduce tariffs across trade routes, resulting in increased costs and customs processing times, as well as slowing international shipping.
FAQ
What is the difference between management and leadership?
Leadership is all about influencing others. Management is all about controlling others.
A leader inspires his followers while a manager directs the workers.
A leader motivates people and keeps them on task.
A leader develops people; a manager manages people.
What is the difference between Six Sigma Six Sigma and TQM?
The key difference between the two quality management tools is that while six-sigma focuses its efforts on eliminating defects, total quality management (TQM), focuses more on improving processes and reducing cost.
Six Sigma stands for continuous improvement. It emphasizes the elimination of defects by using statistical methods such as control charts, p-charts, and Pareto analysis.
This method seeks to decrease variation in product output. This is done by identifying root causes and rectifying them.
Total quality management is the measurement and monitoring of all aspects within an organization. It also includes training employees to improve performance.
It is commonly used as a strategy for increasing productivity.
What are the five management steps?
Planning, execution, monitoring and review are the five stages of any business.
Planning means setting goals for the long-term. This includes setting goals for the future and defining what you want.
Execution takes place when you actually implement the plans. These plans must be adhered to by everyone.
Monitoring is a way to track progress towards your objectives. Regular reviews of performance against budgets and targets should be part of this process.
At the end of every year, reviews take place. They provide an opportunity to assess whether everything went well during the year. If not, then it may be possible to make adjustments in order to improve performance next time.
Evaluation takes place after the annual review. It helps to identify what went well and what didn’t. It also provides feedback on the performance of people.
What is the difference between a project and a program?
A program is permanent, whereas a project is temporary.
A project usually has a specific goal and deadline.
This is often done by a group of people who report to one another.
A program often has a set goals and objectives.
It is typically done by one person.
Statistics
- Your choice in Step 5 may very likely be the same or similar to the alternative you placed at the top of your list at the end of Step 4. (umassd.edu)
- As of 2020, personal bankers or tellers make an average of $32,620 per year, according to the BLS. (wgu.edu)
- The average salary for financial advisors in 2021 is around $60,000 per year, with the top 10% of the profession making more than $111,000 per year. (wgu.edu)
- The BLS says that financial services jobs like banking are expected to grow 4% by 2030, about as fast as the national average. (wgu.edu)
- Hire the top business lawyers and save up to 60% on legal fees (upcounsel.com)
External Links
How To
How do you implement Quality Management Plans (QMPs)?
QMP (Quality Management Plan), introduced in ISO 9001,2008, provides a systematic method for improving processes, products, or services through continuous improvement. It is about how to continually measure, analyze, control, improve, and maintain customer satisfaction.
QMP is a standard way to improve business performance. QMP's goal is to improve service delivery and production. QMPs must include all three elements - Products, Services, and Processes. A "Process" QMP is one that only includes one aspect. QMP stands for Product/Service. QMP stands for Customer Relationships.
There are two key elements to implementing a QMP: Strategy and Scope. These elements can be defined as follows.
Scope is what the QMP covers and how long it will last. If your organization wishes to implement a QMP lasting six months, the scope will determine the activities during the first six month.
Strategy: This is the description of the steps taken to achieve goals.
A typical QMP comprises five phases: Planning and Design, Development, Construction, Implementation, Maintenance. Below is a description of each phase:
Planning: In this stage, the objectives of the QMP are identified and prioritized. Every stakeholder involved in the project is consulted to determine their expectations and needs. After identifying the objectives, priorities, and stakeholder involvement, the next step is to develop the strategy for achieving these objectives.
Design: In this stage, the design team designs the vision and mission, strategies, as well as the tactics that will be required to successfully implement the QMP. These strategies are implemented by the development of detailed plans and procedures.
Development: The development team is responsible for building the resources and capabilities necessary to implement the QMP effectively.
Implementation: This refers to the actual implementation or the use of the strategies planned.
Maintenance: This is an ongoing procedure to keep the QMP in good condition over time.
Several additional items should be added to the QMP.
Stakeholder involvement is important for the QMP's success. They must be involved in all phases of the QMP's development, planning, execution, maintenance, and design.
Project Initiation. It is important to understand the problem and the solution in order to initiate any project. The initiator must know the reason they are doing something and the expected outcome.
Time frame: It is crucial to know the time frame for the QMP. The simplest version can be used if the QMP is only being implemented for a short time. If you're looking to implement the QMP over a longer period of time, you may need more detailed versions.
Cost Estimation. Cost estimation is another crucial component of QMP. Without knowing how much you will spend, planning is impossible. Therefore, cost estimation is essential before starting the QMP.
QMPs are not just a written document. They should be a living document. It changes with the company. It should be reviewed regularly to ensure that it meets current needs.