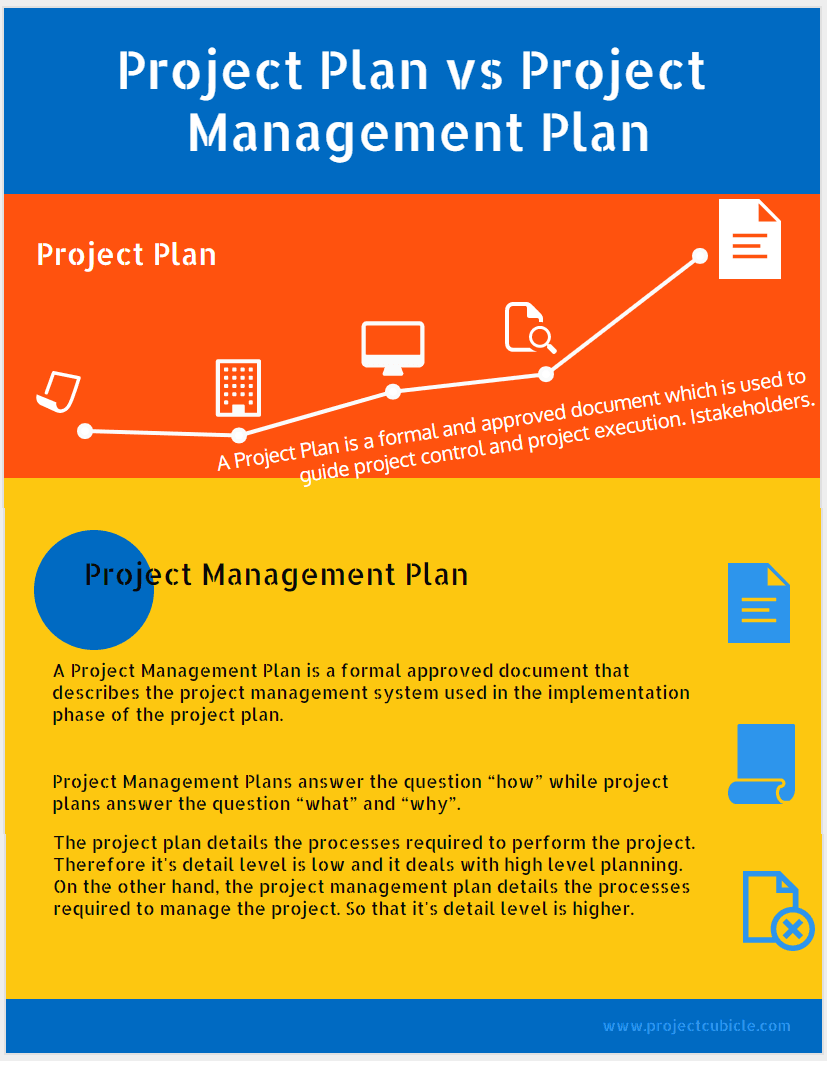
Supply chain management is the management, from raw materials through to the final product. The process involves many interdependent processes that account for a range of risks. These include workforce and company operational dynamics, climate, environmental changes, social, and demographic shifts. To ensure the success of any business, supply chain management must be well-executed.
Manage the flow from raw materials into final products.
Supply chain management is a cross-functional process that oversees the flow of goods from raw materials to finished products. It allows businesses to manage inventory and improve product quality. It can also help increase revenue. A holistic approach to supply chain management can give companies a competitive edge over their competitors.
Planning
During the planning phase, supply chain managers analyze the various factors that can affect the supply chain. These factors include the availability of raw materials, pricing schemes, and the channels through which they are distributed. It is vital that the supply chains are prepared for every possible scenario and that all variables align to meet customer needs. A well-planned supplier chain can reduce costs by eliminating excessive production and waste. It can also help companies deal with limited supply situations.
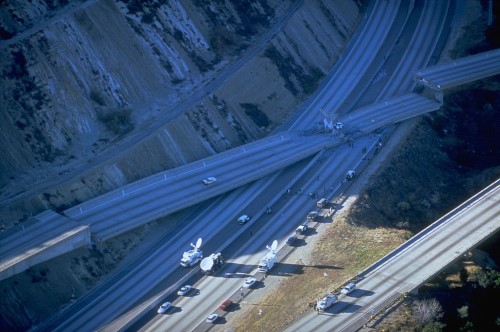
Sourcing
Supply chain management (SCM), is the whole process of delivering products from the raw material to their final destination. It involves demand forecasting, production planning and logistics. All of these factors have a major impact on customer satisfaction and profitability.
Manufacturing
Manufacturing supply chain management focuses on controlling the flow of goods and services in and out of a business. This model allows businesses to increase productivity and efficiency while decreasing the cost of labor and materials. Optimized supply chain management is also a way to ensure that a company's infrastructure is planned in the best interest.
Delivery
The delivery component is key to supply chain management. It involves receiving and storing products as well retrieving them and preparing them for dispatch. This process is crucial to the viability and success of delivery. Proper planning and information flow between departments can improve delivery performance and minimize logistical expense.
Returns
Returns management can be implemented in an organization or within a supply network to reduce unwanted product flows. This process can be implemented to improve operational efficiencies. This involves many sub-processes. These activities are also interdependent with other supply chain management processes.
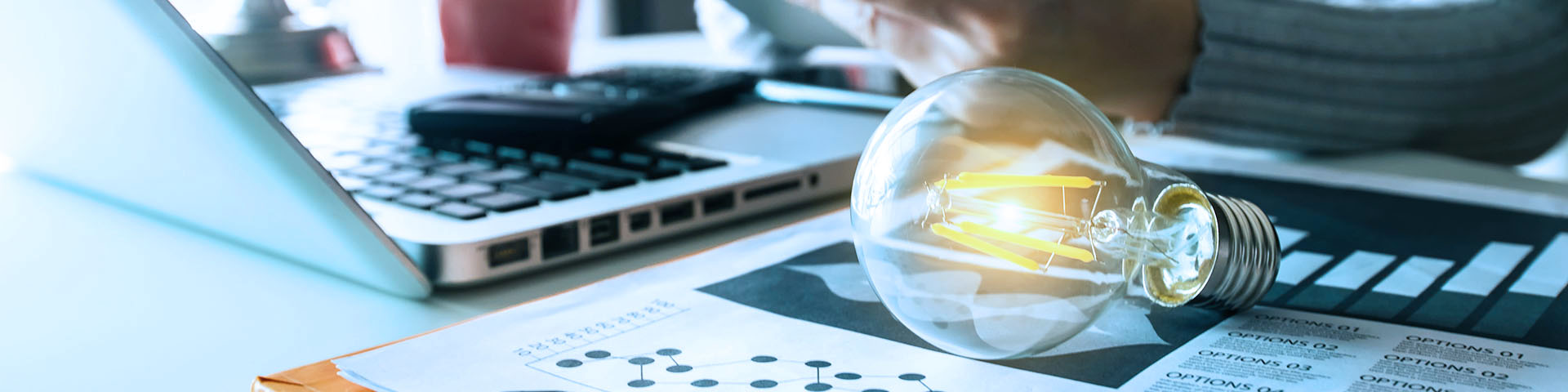
Control of costs
Supply chain management cannot be done without cost control. It helps to keep the supply chain's overall costs within budget. It also helps determine how to allocate costs across the supply chain. The cost analysis is not only useful in determining how to allocate the costs but also helps to improve competitiveness.
FAQ
What is TQM?
The industrial revolution led to the birth and growth of the quality movement. Manufacturing companies realized they couldn't compete solely on price. To remain competitive, they had to improve quality as well as efficiency.
Management responded to the need to improve, and developed Total Quality Management (TQM). This focused on improving every aspect of an organization’s performance. It included continuous improvement, employee involvement and customer satisfaction.
What is Kaizen and how can it help you?
Kaizen is a Japanese term which means "continuous improvement." This philosophy encourages employees to continually look for ways to improve the work environment.
Kaizen is built on the belief that everyone should be able do their jobs well.
What does Six Sigma mean?
Six Sigma employs statistical analysis to identify problems, measure them and analyze root causes. Six Sigma also uses experience to correct problems.
The first step in solving a problem is to identify it.
Next, data are collected and analyzed in order to identify patterns and trends.
The problem is then rectified.
Finally, data will be reanalyzed to determine if there is an issue.
This cycle continues until there is a solution.
Why is project management so important?
To ensure projects run smoothly and meet deadlines, project management techniques are employed.
This is because most businesses rely heavily on project work to produce goods and services.
These projects must be managed efficiently and effectively by companies.
Without effective project management, companies may lose money, time, and reputation.
Six Sigma is so popular.
Six Sigma can be implemented quickly and produce impressive results. It also provides a framework for measuring improvements and helps companies focus on what matters most.
What is a basic management tool that can be used for decision-making?
A decision matrix, a simple yet powerful tool for managers to make decisions, is the best. It helps them to think strategically about all options.
A decision matrix allows you to represent alternatives as columns and rows. This allows one to see how each alternative impacts other options.
In this example, we have four possible alternatives represented by the boxes on the left side of the matrix. Each box represents one option. The top row depicts the current status quo, while the bottom row represents what would happen if no action was taken.
The middle column shows the effect of choosing Option 1. In this case, it would mean increasing sales from $2 million to $3 million.
The results of choosing Option 2 and 3 can be seen in the columns below. These are good changes, they increase sales by $1million or $500,000. However, these also involve negative consequences. Option 2 increases costs by $100 thousand, while Option 3 decreases profits to $200 thousand.
The last column displays the results of selecting Option 4. This will result in sales falling by $1,000,000
The best part of using a decision-matrix is that it doesn't require you to know which numbers belong where. The best thing about a decision matrix is that you can simply look at the cells, and immediately know whether one option is better or not.
The matrix already does all the work. It is as simple as comparing the numbers within the relevant cells.
Here's an example showing how you might use a Decision Matrix in your business.
You need to decide whether to invest in advertising. This will allow you to increase your revenue by $5000 per month. However, this will mean that you'll have additional expenses of $10,000.
If you look at the cell that says "Advertising", you can see the number $15,000. Advertising is worth much more than the investment cost.
Statistics
- The BLS says that financial services jobs like banking are expected to grow 4% by 2030, about as fast as the national average. (wgu.edu)
- The profession is expected to grow 7% by 2028, a bit faster than the national average. (wgu.edu)
- As of 2020, personal bankers or tellers make an average of $32,620 per year, according to the BLS. (wgu.edu)
- Our program is 100% engineered for your success. (online.uc.edu)
- This field is expected to grow about 7% by 2028, a bit faster than the national average for job growth. (wgu.edu)
External Links
How To
How can Lean Manufacturing be done?
Lean Manufacturing methods are used to reduce waste through structured processes. They were developed in Japan by Toyota Motor Corporation (in the 1980s). The main goal was to produce products at lower costs while maintaining quality. Lean manufacturing emphasizes removing unnecessary steps from the production process. It is made up of five elements: continuous improvement, continuous improvement, just in-time, continuous change, and 5S. Pull systems are able to produce exactly what the customer requires without extra work. Continuous improvement is the continuous improvement of existing processes. Just-in-time refers to when components and materials are delivered directly to the point where they are needed. Kaizen means continuous improvement. Kaizen involves making small changes and improving continuously. Fifth, the 5S stand for sort, set up in order to shine, standardize, maintain, and standardize. To achieve the best results, these five elements must be used together.
Lean Production System
Six key concepts are the basis of lean production:
-
Flow: The goal is to move material and information as close as possible from customers.
-
Value stream mapping - break down each stage of a process into discrete tasks and create a flowchart of the entire process;
-
Five S’s - Sorted, In Order. Shine. Standardize. And Sustain.
-
Kanban - visual cues such as stickers or colored tape can be used to track inventory.
-
Theory of constraints: Identify bottlenecks and use lean tools such as kanban boards to eliminate them.
-
Just-in time - Get components and materials delivered right at the point of usage;
-
Continuous improvement - incremental improvements are made to the process, not a complete overhaul.